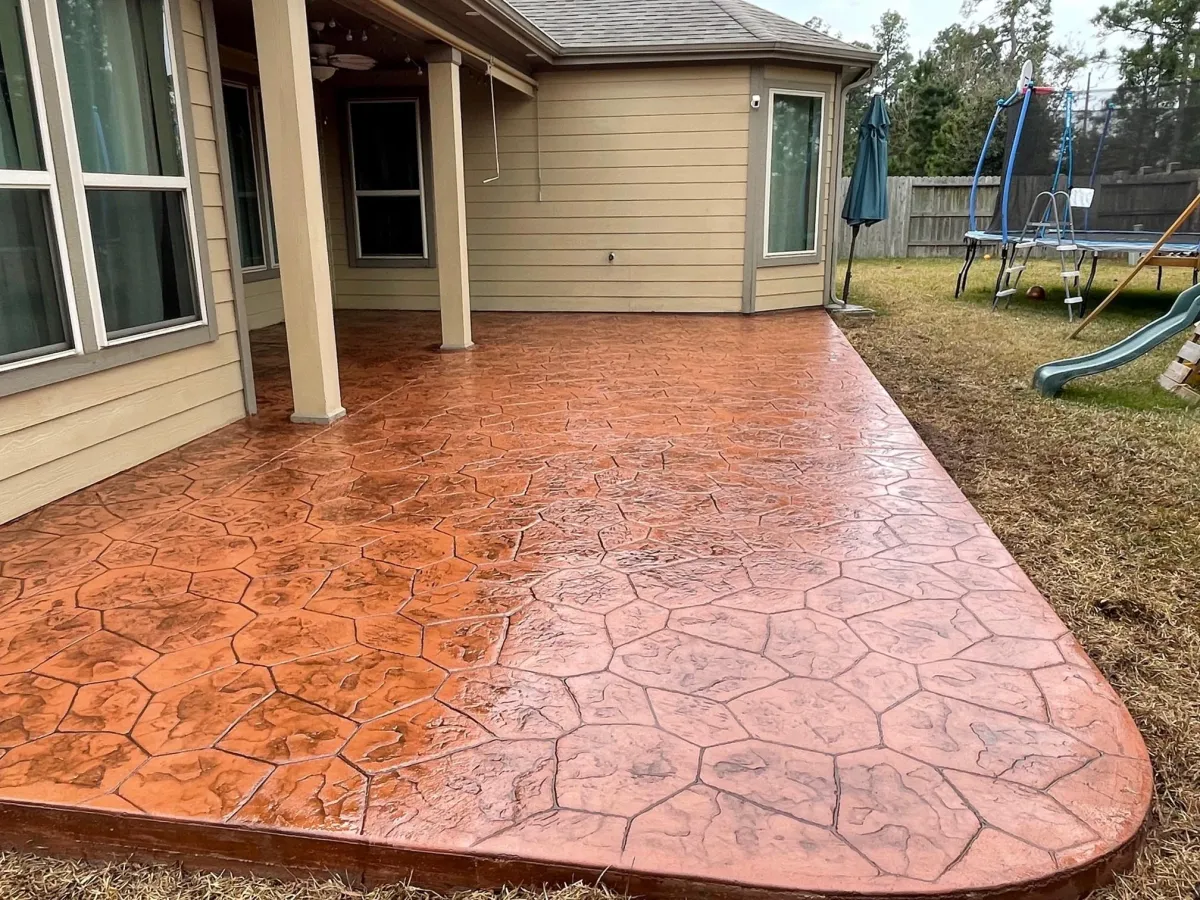
How thick should a concrete patio be?
How Thick Should a Concrete Patio Be?
For most residential concrete patios, a thickness of 4 inches (10 cm) is generally sufficient. This depth provides adequate strength and durability for typical uses. Such uses include supporting patio furniture, grills, and regular foot traffic.
However, this is a baseline recommendation. Certain conditions or intended uses may necessitate a thicker slab. Factors like heavy loads, challenging soil conditions, or the presence of vehicles can require a minimum of 5 or even 6 inches of concrete.
The "right" thickness is ultimately a balance. It must meet the structural demands of your specific project. It should also be cost-effective, avoiding unnecessary material and labor.
Professional assessment is key. Experienced concrete patio contractors can accurately determine the ideal thickness for your unique situation.
Understanding the Factors Influencing Patio Thickness
Determining the appropriate thickness for a concrete patio involves more than just a standard measurement. Several critical factors come into play. Each one contributes to the structural integrity and longevity of the slab. Ignoring any of these can lead to costly problems.
1. Intended Use and Load Bearing
The primary consideration for patio thickness is how you plan to use the space. The weight it will support dictates its structural requirements.
Light Foot Traffic/Patio Furniture (4 inches):
For standard residential patios, a 4-inch slab is typically robust enough.
It can comfortably bear the weight of outdoor tables, chairs, lounge furniture, and barbecue grills.
The forces at play are relatively low, consisting mainly of distributed weight. This minimal thickness provides sufficient compressive strength for these static loads.
This is the most economical choice for a functional patio.
Heavy Furniture/Hot Tubs/Outdoor Kitchens (5 inches):
If your patio will host heavier items, increasing the thickness to 5 inches is a wise investment.
Hot tubs, large outdoor kitchen islands with appliances, or substantial masonry fire pits exert concentrated, heavy loads.
A 5-inch slab provides extra structural integrity. It helps distribute these significant weights more effectively over the sub-base. This prevents localized settling or cracking under stress.
It also offers increased resistance to dynamic loads, such as people moving around a hot tub.
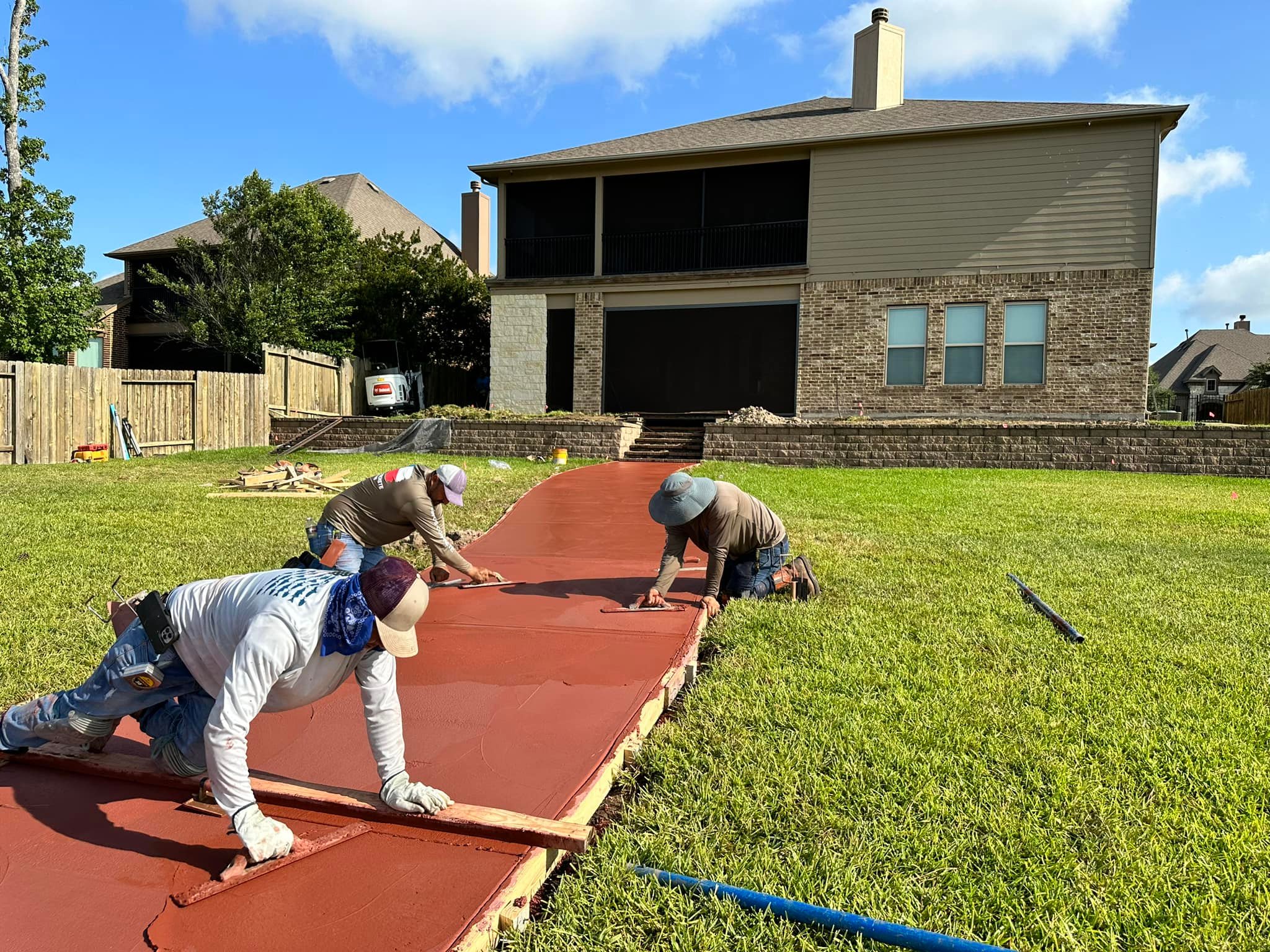
Occasional Vehicle Traffic (6 inches+):
If your patio might double as a parking area, or if you plan to drive a heavy lawnmower or light vehicle across it occasionally, 6 inches of concrete is advisable.
The concentrated weight and movement of vehicles create much higher stresses on the slab.
For a dedicated driveway or frequent vehicle traffic, 6 inches with heavy-duty reinforcement (rebar) is the minimum. Some commercial applications or very heavy vehicles might even require 8 inches or more.
A patio not designed for vehicle loads will fail if consistently subjected to them.
Matching thickness to anticipated load is crucial. Under-engineering leads to failure, while over-engineering wastes resources.
2. Soil Conditions and Sub-Base Preparation
The ground beneath your patio is its ultimate foundation. The stability and type of soil profoundly affect how thick the concrete needs to be.
Ideal Soil:
Stable, well-draining granular soils (sandy, gravelly) are ideal. They provide uniform support and are less prone to movement.
In such conditions, a standard 4-inch slab with proper preparation can perform excellently.
Problematic Soils (Expansive Clay in Houston):
Houston, Texas, is renowned for its expansive clay soils. These soils are a significant challenge for concrete construction.
Expansive clay swells dramatically when wet and shrinks when dry. This constant volume change exerts immense pressure on concrete slabs, leading to heaving (lifting) and cracking.
Mitigation Methods for Expansive Clay:
Deeper Excavation: Sometimes, more soil is removed than usual.
Thicker, Well-Compacted Granular Sub-Base: A sub-base of 6-8 inches (or more) of thoroughly compacted gravel or crushed stone is critical. This acts as a buffer layer. It minimizes the direct impact of soil movement on the slab. It also provides superior drainage.
Moisture Barriers: A polyethylene vapor barrier placed over the compacted sub-base can help prevent moisture from migrating from the soil into the concrete. This helps stabilize moisture content.
Enhanced Reinforcement: Even with a good sub-base, heavy steel rebar is often preferred over wire mesh in expansive clay areas. It provides superior structural integrity to withstand soil forces.
Drainage: Meticulous attention to surface and subsurface drainage around the patio is paramount. This prevents excessive water accumulation in the expansive clay.
Crucial Point: In expansive clay, a slightly thicker slab (e.g., 5 inches instead of 4) combined with superior sub-base preparation and robust reinforcement is often far more effective and durable than merely adding thickness without addressing the soil's inherent issues. A thick slab on an unstable base will still fail.
Compaction:
Regardless of soil type, the native soil base and any added sub-base material must be uniformly compacted.
Proper compaction eliminates air pockets. It creates a dense, stable foundation. Skipping this step leads to uneven settling and cracking, regardless of slab thickness.
Understanding your soil is as important as choosing the right thickness.
3. Reinforcement Type
Reinforcement adds tensile strength to concrete. It helps the slab resist cracking and hold together if cracks do form. It allows concrete to perform better under stress.
Wire Mesh:
Commonly used in 4-inch slabs for crack control. It helps distribute shrinkage cracks into smaller, less noticeable patterns.
It offers limited structural strength against significant bending or settling forces. It is not designed to prevent major structural cracking.
Must be properly elevated within the concrete (middle third of the slab).
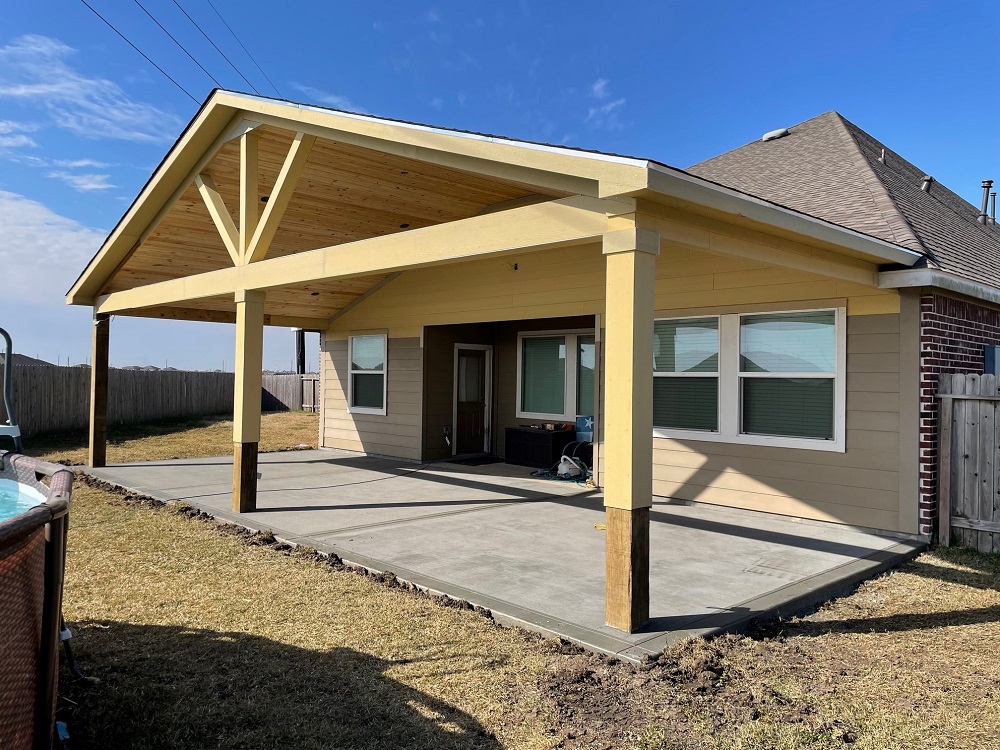
Rebar (Steel Reinforcing Bar):
Provides superior structural strength and is highly recommended for 5-inch or 6-inch slabs.
It significantly increases the slab's ability to withstand heavier loads and resist forces from problematic soils (like Houston's expansive clay).
A grid pattern (e.g., #3 rebar on 18-24 inch centers) is tied together.
Like mesh, rebar must be correctly positioned within the slab (typically the bottom third, where tensile forces are highest).
Fibers:
Synthetic or steel fibers can be added to the concrete mix. They help reduce plastic shrinkage cracking during the initial curing phase.
They are typically used as a supplement to mesh or rebar, not a replacement.
The type and proper placement of reinforcement enhance the slab's performance. This allows a given thickness to withstand more stress.
4. Climate and Drainage
Environmental factors, particularly water, greatly influence a concrete patio's longevity and thus impact thickness considerations.
Freeze-Thaw Cycles (Less relevant for Houston):
In colder climates, water absorbed by concrete can freeze and expand, causing spalling (surface flaking) and deterioration.
Proper drainage, air-entrained concrete (which contains microscopic air bubbles to relieve internal pressure), and adequate slab thickness are vital here. While not a primary concern for Houston, general principles of water management remain crucial.
Heavy Rainfall (Highly relevant for Houston):
Houston experiences significant rainfall. Poor drainage around a concrete patio can lead to water pooling on the surface or, worse, saturating the underlying soil.
Excessive moisture can erode the sub-base, leading to voids and uneven settling. This compromises the slab's integrity regardless of its thickness.
Crucial Aspect: Your patio must be sloped away from your house at a minimum of 1/4 inch per foot. This ensures surface water runs off efficiently.
Consider integrating drainage systems like trench drains or catch basins in areas prone to heavy runoff. This prevents hydrostatic pressure and protects the slab and adjacent structures.
Proper water management through grading and drainage is as important as slab thickness. It ensures long-term stability.
5. Concrete Mix Strength (PSI)
Concrete strength is measured in pounds per square inch (PSI). This rating indicates the concrete's compressive strength after 28 days of curing.
2500-3000 PSI: Common for general residential patios with light loads. A 4-inch slab with this strength is usually sufficient for typical patio use.
3500-4000 PSI: Recommended for patios supporting heavier loads (hot tubs, outdoor kitchens) or experiencing occasional vehicle traffic. It provides extra durability and crack resistance.
Higher PSI concrete costs more per cubic yard. The choice of PSI should align with the slab's thickness and intended use. Sometimes, a slightly higher PSI concrete can offer added resilience to a 4-inch slab for standard patio use.
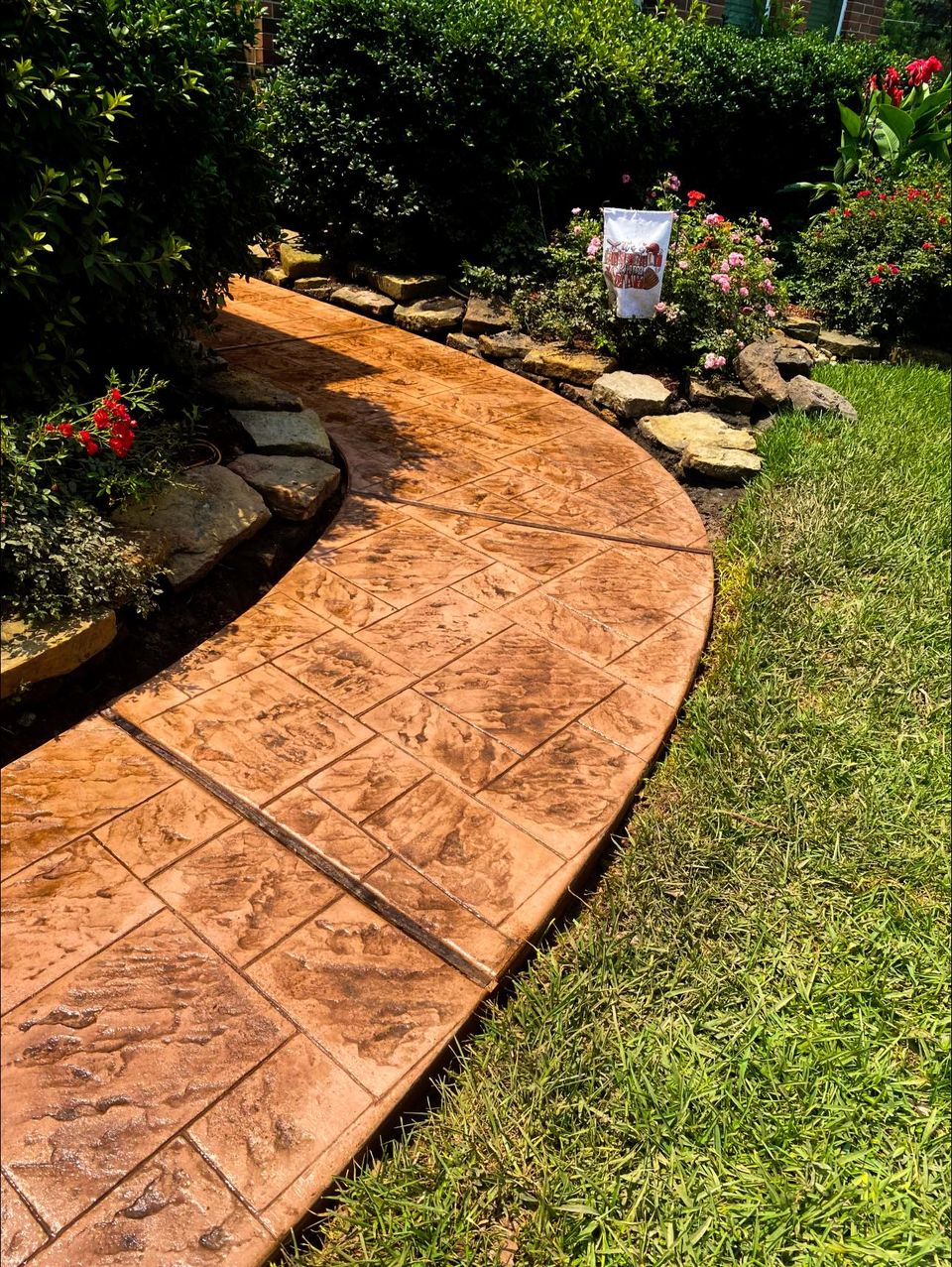
A well-chosen concrete mix complements the slab thickness. It contributes to overall strength and longevity.
The Implications of Incorrect Thickness
Choosing the wrong thickness for your concrete patio can have significant long-term consequences. Both being too thin or unnecessarily thick present their own set of problems.
Too Thin (Under-Engineered)
An under-engineered patio is a false economy. Any initial cost savings will likely be dwarfed by future expenses.
Premature Cracking, Spalling, and Deterioration: A slab that is too thin cannot adequately handle the loads placed upon it or the forces from soil movement. It will crack prematurely, leading to unsightly and potentially hazardous surface issues. Spalling (flaking) can also occur if the surface integrity is compromised.
Settling and Uneven Surfaces: Without sufficient thickness or proper base support, the slab can settle unevenly. This creates dips, humps, and poor drainage, leading to standing water.
Structural Failure: Under heavy, sustained loads, an undersized slab can suffer catastrophic structural failure. This means large sections may break apart or collapse.
Costly Repairs or Full Replacement: Fixing a significantly damaged, too-thin patio often involves expensive crack injections, resurfacing, or even complete demolition and repour. These costs quickly negate any initial savings.
The long-term cost of a patio that fails early is far greater than the minor savings achieved by reducing its thickness.
Too Thick (Over-Engineered)
While a thicker patio will undoubtedly be stronger, making it unnecessarily thick is not a cost-effective solution.
Unnecessary Material Cost: Every extra inch of thickness means significantly more concrete volume. This directly translates to higher material costs for the concrete itself.
Increased Labor for Excavation and Pouring: A thicker slab requires deeper excavation. It also means more cubic yards of concrete to spread, screed, and finish. This increases labor hours and associated costs.
Higher Disposal Costs (if removed later): If the patio ever needs to be removed (e.g., for future renovation), a thicker slab is heavier and more challenging to break up. This increases demolition and debris disposal fees.
Not Cost-Efficient: While it offers ultimate durability, if the extra strength isn't genuinely needed for the patio's intended use and soil conditions, it's an inefficient use of resources.
The goal is to find the optimal thickness, providing necessary strength without overspending.
Site Preparation: Crucial for Any Thickness
Regardless of how thick your concrete patio will be, the quality of its site preparation is paramount. Even the thickest slab will fail if built on an unstable or poorly prepared foundation. This phase represents a significant portion of the project's success and longevity.
Importance of a Solid Foundation
Load Distribution: A well-prepared sub-base uniformly distributes the weight of the concrete slab and its loads over a larger area. This prevents localized pressure points.
Drainage: Proper grading and a granular sub-base prevent water from accumulating under the slab. This avoids erosion, freeze-thaw damage (in colder climates), and soil saturation.
Stability: A dense, compacted sub-base minimizes future settling or shifting of the slab.
A concrete patio is only as good as the ground it rests upon.
Demolition and Clearing
Remove Obstacles: The first step is to thoroughly clear the area. This includes removing any vegetation, tree roots, old paving, or existing structures.
Proper Disposal: All debris must be hauled away properly. This ensures a clean and unhindered workspace for the subsequent steps.
A clean site is fundamental for accurate preparation.
Excavation and Compaction
Precise Depth: The area must be excavated to the precise depth required for the chosen slab thickness plus the sub-base (e.g., 4" slab + 4-6" gravel = 8-10" total excavation depth).
Native Soil Compaction: After excavation, the underlying native soil must be uniformly compacted. This creates a firm base and prevents future settling.
Addressing Problematic Soils (Houston): In areas with expansive clay like Houston, special attention is needed. This might include removing more problematic soil and replacing it with engineered fill or a deeper sub-base.
Thorough compaction is vital for long-term stability.
Sub-Base Installation and Compaction
Material: A layer of clean, granular material like gravel or crushed stone is spread over the compacted native soil. A minimum of 4 inches is generally recommended, often 6 inches or more for heavier loads or problematic soils.
Layering and Compaction: The sub-base material should be placed in lifts (layers) of 2-4 inches. Each lift must be thoroughly compacted using a vibratory plate compactor. This achieves maximum density.
Moisture: The sub-base should be slightly moist during compaction. This aids in achieving proper density.
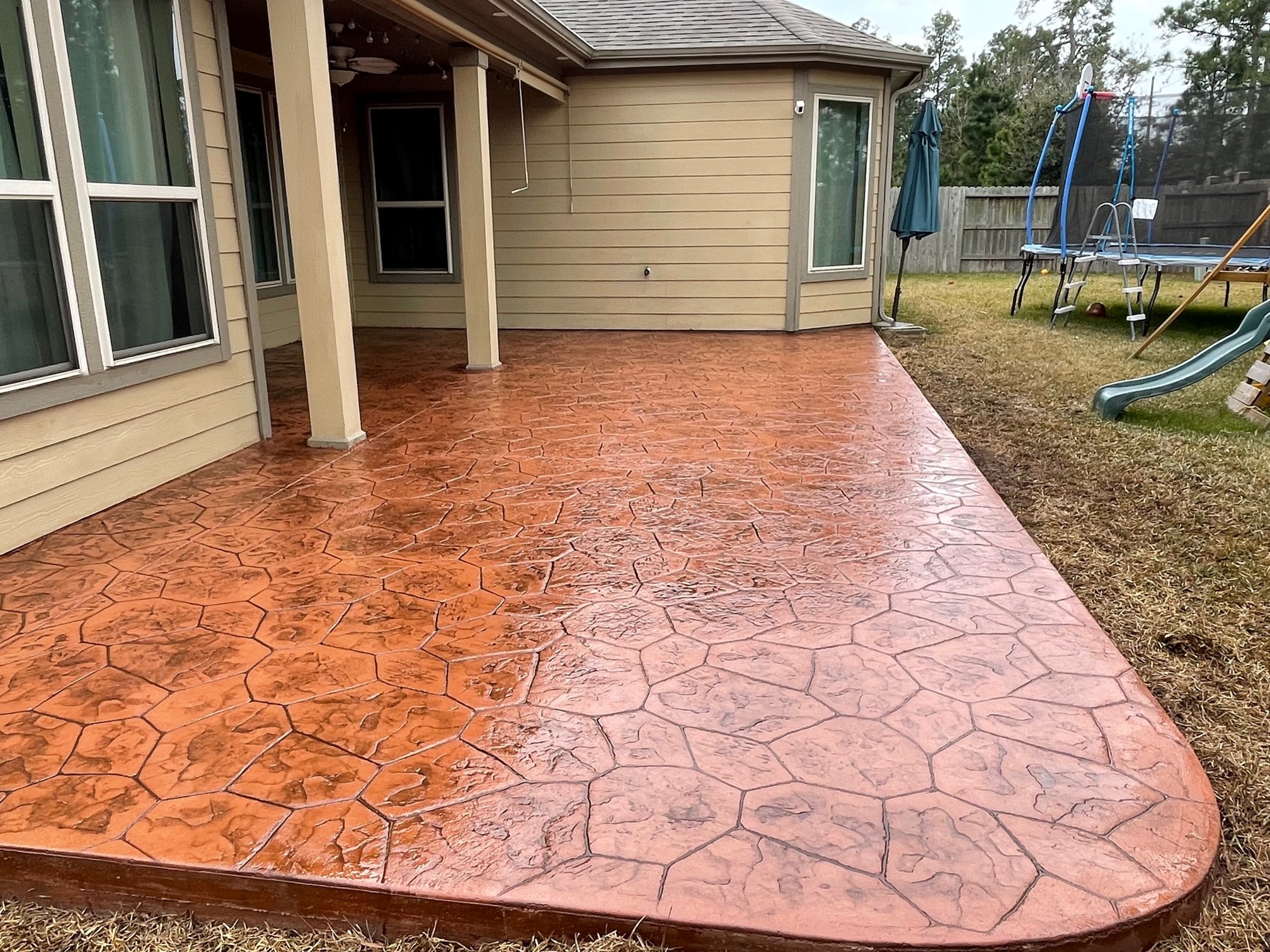
A properly installed and compacted sub-base acts as a stable, well-draining buffer beneath the concrete.
Formwork
Perimeter Definition: Sturdy forms (typically lumber) are installed around the perimeter of the excavated area. These define the exact dimensions and intended thickness of your patio.
Leveling and Bracing: The forms must be perfectly level (or sloped for drainage) and securely braced. This prevents them from bowing or shifting when the heavy concrete is poured.
Accurate formwork ensures a uniformly thick and shaped slab.
Vapor Barrier (Optional but Recommended in Some Cases)
A heavy-duty polyethylene vapor barrier can be placed over the compacted sub-base, under the concrete.
Purpose: It acts as a moisture retarder. It prevents moisture from rising from the ground and migrating into the concrete or through the slab. This can help prevent efflorescence (white mineral deposits) and moisture-related issues, especially under covered patios or if you intend to add flooring/coatings later.
A vapor barrier is a relatively low-cost addition with long-term benefits for moisture control.
Professional Guidance: The Best Way to Determine Thickness
Given the numerous variables involved, relying on the expertise of professional concrete patio contractors is the most reliable way to determine the ideal thickness for your patio. Their experience ensures a durable and code-compliant installation.
Why Consult Concrete Patio Contractors
Local Knowledge: Experienced contractors intimately understand local soil conditions. In Houston, they are familiar with expansive clay. They know the best practices for mitigating its effects.
Building Codes: They are up-to-date on local building codes and regulations. These codes may specify minimum thicknesses or reinforcement requirements for certain types of concrete slabs or uses.
Load Assessment: They can accurately assess the loads your patio will bear. They recommend the appropriate thickness and reinforcement to handle those loads safely.
Site-Specific Challenges: They can identify and propose solutions for unique site challenges, such as steep slopes, poor drainage, or existing utility lines.
A professional's assessment is invaluable for a long-lasting patio.
Soil Testing (for Complex Projects or Very Bad Soils)
For very large patios, those supporting extremely heavy loads, or properties with unusually problematic soil conditions, a geotechnical engineer may be consulted.
Purpose: A soil test provides detailed information about the soil's composition, bearing capacity, and expansion potential. This data allows for precise engineering recommendations.
While an added cost, soil testing can be a wise investment for complex projects to avoid future failure.
Local Building Codes in Houston
The City of Houston and surrounding counties have specific building codes. These might dictate minimum requirements for concrete flatwork, especially for larger structures or those built within certain zones.
Permits: Large concrete patios might require permits. Contractors are typically responsible for ensuring the project adheres to these codes and secures necessary permits.
Minimums: Codes might specify minimum slab thickness, concrete strength, or reinforcement for specific applications (e.g., driveway aprons, accessory building foundations).
A reputable contractor will ensure your patio meets all local regulatory standards.
Benefits of Hiring a Pro
Hiring a professional for your concrete patio project, including determining thickness, offers numerous benefits:
Correct Thickness and Design: They ensure the right thickness is chosen and all other design elements (sub-base, reinforcement, drainage) are correctly specified.
Proper Installation: Expertise in site preparation, pouring, finishing, and curing guarantees a high-quality outcome.
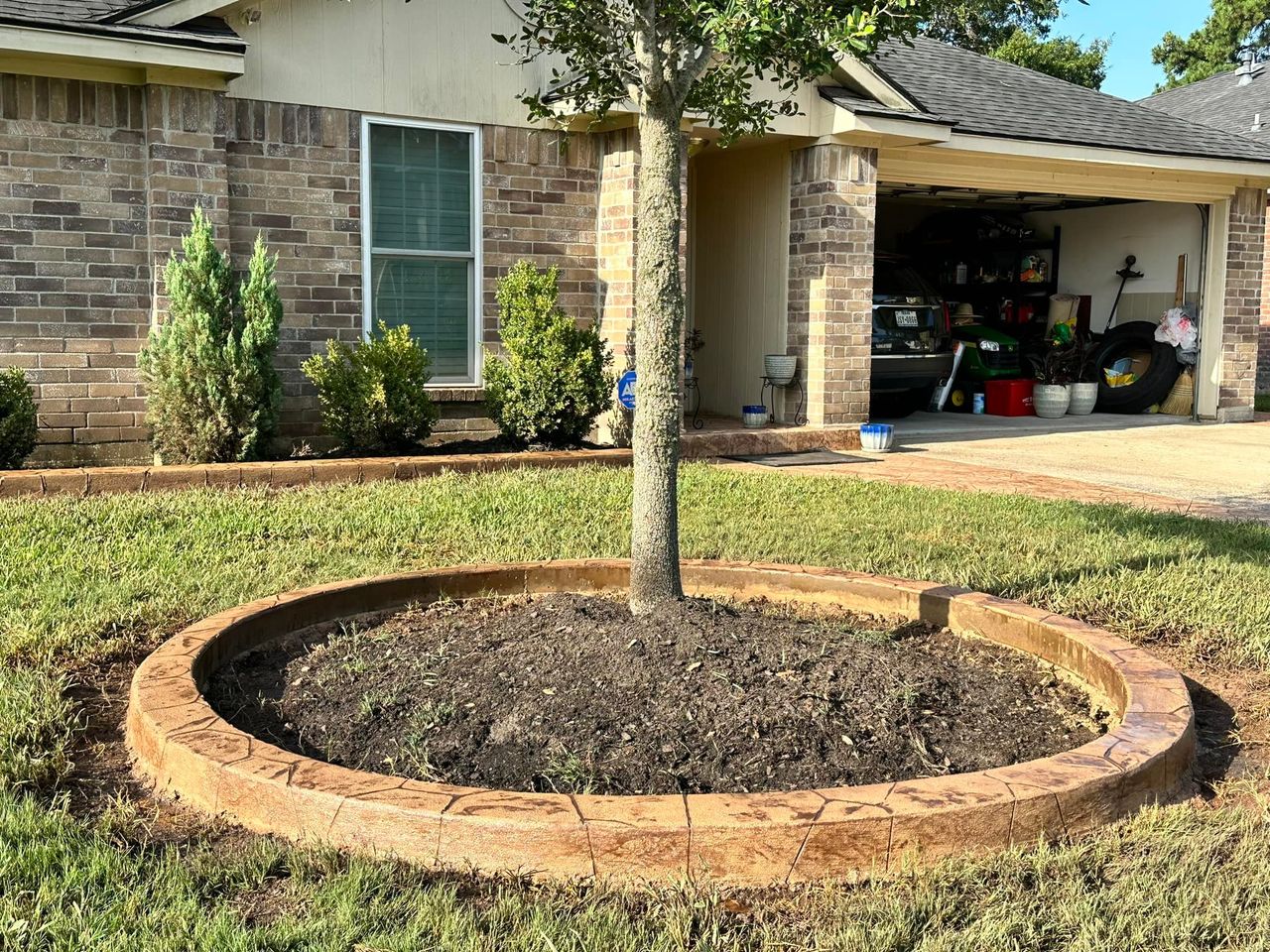
Warranty: Most reputable contractors offer a warranty on their workmanship, providing peace of mind.
Cost Efficiency: While a professional costs more upfront, they prevent costly mistakes, re-dos, and premature failures. This makes them more cost-effective in the long run.
In Houston, Texas, reputable concrete patio contractors like Cincos Concrete LLC understand these intricacies. They ensure your patio is built to last.
Cost Implications of Slab Thickness
The thickness of your concrete patio directly impacts the overall project cost. Understanding these financial implications is crucial for accurate budgeting.
Material Costs
Concrete Volume: Every additional inch of thickness significantly increases the cubic yardage of concrete required. Concrete is a major material expense.
Linear Relationship: The cost of concrete material generally increases linearly with thickness. A 5-inch slab will require 25% more concrete than a 4-inch slab for the same area, and a 6-inch slab will require 50% more.
This direct relationship makes thickness a primary cost driver.
Labor Costs
Excavation: A thicker slab requires deeper excavation. This means more soil to remove, increasing labor hours and potentially equipment rental (e.g., mini-excavator).
Pouring and Finishing: More concrete volume takes more time for the crew to spread, screed, float, and finish before it sets. This translates to increased labor hours.
Reinforcement Installation: If a thicker slab requires more complex reinforcement (e.g., rebar grid vs. wire mesh), this adds to the labor for cutting, tying, and positioning.
More material typically means more labor.
Reinforcement Costs
Wire Mesh vs. Rebar: As thickness increases, so does the likelihood that you'll need more robust (and expensive) reinforcement. Rebar costs more per square foot than wire mesh.
Density of Rebar: If a denser rebar grid is specified for a thicker slab, this further increases material and labor costs.
The type of reinforcement chosen complements the slab's thickness.
Site Preparation Costs
Deeper Digging: If a thicker slab means deeper initial excavation, it can lead to higher costs for earth moving and potentially dirt disposal.
Increased Sub-Base: A thicker slab often pairs with a deeper sub-base. This adds material costs for gravel and labor for spreading and compaction.
The entire foundation must be proportionally robust.
Long-Term Savings
While a thicker, better-engineered patio has a higher upfront cost, it represents a significant long-term saving.
Reduced Repairs: A properly built slab with the correct thickness and preparation is far less likely to crack, settle, or deteriorate prematurely. This eliminates expensive future repair or replacement costs.
Increased Lifespan: Investing in the correct thickness means your patio will last for decades, providing value for a longer period.
The initial investment for proper thickness and preparation yields substantial returns over the patio's lifespan.
Installation Quality Beyond Thickness
While choosing the correct thickness is vital, it's only one piece of the puzzle. The quality of the concrete mix and the installation process itself are equally important for the overall success and durability of your patio. A thick slab poorly installed will still fail.
Proper Concrete Mix and Slump
Specified PSI: Ensure your contractor orders the concrete mix with the correct PSI rating for your intended use and slab thickness.
Correct Slump: Slump refers to the wetness or consistency of the concrete. The right slump ensures workability without compromising strength. Too wet concrete is weaker.
The right mix design contributes directly to the slab's strength.
Placement and Screeding
Uniform Thickness: The concrete must be uniformly placed within the forms. Skilled screeding ensures that the concrete reaches the exact specified thickness across the entire slab. Inconsistent thickness creates weak spots.
Efficiency: Rapid and efficient placement is crucial for larger slabs. This prevents cold joints and allows for proper finishing before the concrete stiffens too much.
Accurate placement is fundamental to achieving the designed thickness.
Finishing Techniques
Floating and Troweling: Proper floating and troweling densify the concrete surface, making it more durable and resistant to wear. They also achieve the desired surface texture (e.g., broom finish for slip resistance).
Skilled Finishers: Achieving a high-quality finish requires experienced concrete finishers. They know the correct timing for each step as the concrete sets.
The finish impacts both the appearance and the surface durability.
Control Joints and Expansion Joints
Control Joints: These are strategically placed cuts or grooves in the concrete. They create weak planes where cracks are encouraged to form in a controlled, straight line. For large patios, proper spacing of control joints is critical to prevent random cracking.
Expansion Joints: These are full-depth separations in the concrete. They are used where the patio meets other structures (like a house foundation or existing driveway) to allow for independent movement. This prevents cracking caused by differential expansion and contraction.
These joints are essential for managing concrete's natural tendency to crack.
Curing
Moisture Management: After placement and initial finishing, the concrete must be properly cured. This involves keeping it moist for several days (typically 3-7 days minimum, but ideally 28 days for full strength development).
Methods: Common curing methods include covering with plastic sheeting, continuous misting, or applying a liquid curing compound.
Importance: Proper curing allows the concrete to hydrate fully, achieving its designed strength and hardness. Skipping or shortening the curing process significantly weakens the concrete. It makes it more susceptible to cracking, dusting, and early deterioration.
Curing is arguably the most vital step after the pour for long-term performance.
Sealing
Protection: After the concrete has fully cured, applying a quality concrete sealer is highly recommended. Sealers protect the surface from moisture penetration, stains, UV damage, and everyday wear.
Frequency: Reapplication is typically needed every 2-5 years, depending on traffic and product.
Sealing is a low-cost maintenance step that extends the patio's life and keeps it looking good.
Common Patio Scenarios and Recommended Thickness (Houston Context)
Let's look at specific patio scenarios and corresponding thickness recommendations, keeping Houston's unique conditions in mind.
Basic Patio (Chairs, Grill)
Recommendation: 4 inches (10 cm) with at least wire mesh reinforcement.
Houston Specific: Ensure excellent sub-base preparation (minimum 4-6 inches of compacted gravel). Proper grading for drainage is non-negotiable due to heavy rainfall. Even for light use, considering rebar over mesh might be a wise investment in areas with highly reactive clay soils, as advised by your concrete patio contractors.
This is the most common and cost-effective option for simple outdoor living.
Patio with Hot Tub/Outdoor Kitchen
Recommendation: 5 inches (12.5 cm) with steel rebar reinforcement.
Houston Specific: The increased load requires a very robust sub-base, potentially thicker (6-8 inches) and meticulously compacted. The rebar is crucial to distribute the concentrated weight of a filled hot tub or heavy outdoor kitchen structures. Professional soil assessment might be prudent for very heavy setups.
The added thickness and reinforcement are vital for supporting significant weight.
Patio with Occasional Vehicle Access (e.g., for lawnmower access or light vehicle parking)
Recommendation: 5 to 6 inches (12.5 - 15 cm) with steel rebar reinforcement.
Houston Specific: A 6-inch slab with rebar is ideal for any consistent vehicle traffic. The sub-base must be exceptionally well-prepared and compacted to withstand the dynamic loads from vehicles. Excellent drainage is paramount to prevent sub-base erosion and soil saturation under traffic.
Any vehicle traffic necessitates a substantial increase in slab strength.
Dealing with Houston's Expansive Clay
Regardless of the exact thickness chosen, the presence of expansive clay in Houston dictates a more rigorous approach to patio construction:
Deep and Compacted Sub-Base: This is the most critical element.
Robust Reinforcement: Rebar is often preferred over wire mesh to provide structural integrity against soil movement.
Moisture Management: Meticulous grading and potentially subsurface drainage solutions are essential to minimize water absorption by the clay.
Professional Consultation: Always consult with experienced local concrete patio contractors. They understand the nuances of building on Houston's challenging soils. They can recommend the most appropriate thickness and construction methods. For example, Cincos Concrete LLC would be well-versed in these requirements.
Proper mitigation for expansive soils is a key factor in ensuring your patio's longevity in Houston.
Conclusion
The ideal thickness for a concrete patio is not a one-size-fits-all answer. While 4 inches is a common baseline for most residential uses, the precise depth should be determined by several critical factors: the patio's intended use and the loads it will bear, the specific soil conditions (especially problematic expansive clay found in Houston), the type of reinforcement used, and climate considerations like heavy rainfall.
Under-engineering the thickness leads to premature failure and costly repairs, while over-engineering wastes resources. Crucially, even the correct thickness will fail without meticulous site preparation, including proper excavation, a well-compacted sub-base, and effective drainage.
For any concrete patio project, particularly in areas with challenging soil like Houston, consulting with experienced concrete patio contractors is invaluable. They possess the local knowledge, expertise, and equipment to assess your specific needs, recommend the optimal thickness and design, and ensure a professional, durable installation. This expert guidance, whether from general contractors or specialized concrete patio contractors like Cincos Concrete LLC, is the best investment for a long-lasting and trouble-free concrete patio.