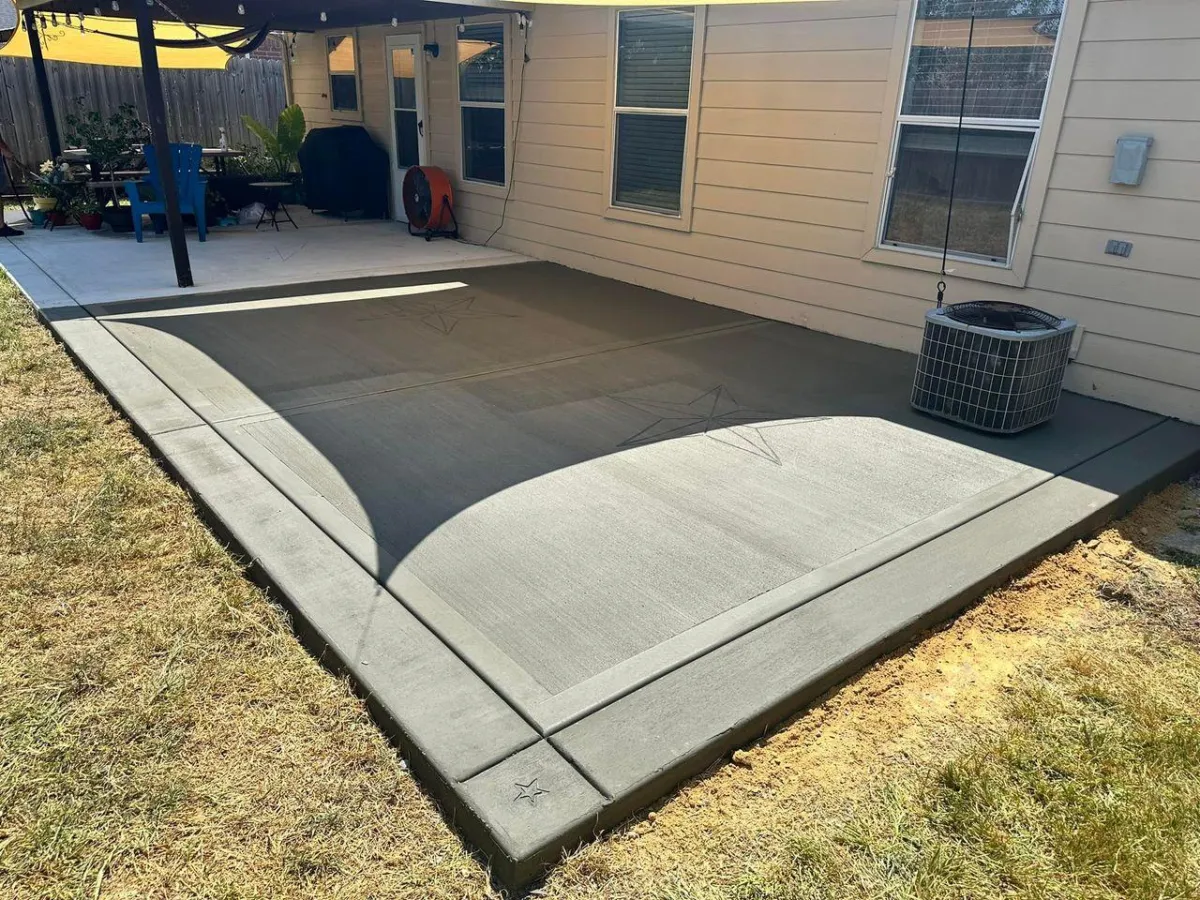
How much concrete for a 30x40 slab 4 inches thick?
How Much Concrete for a 30x40 Slab 4 Inches Thick?
For a 30x40 foot concrete slab that is 4 inches thick, you will need a substantial amount of concrete. This large area totals 1200 square feet, requiring a precise volume calculation.
The calculation for a slab of this dimension and thickness is as follows:
Area: 30 feet * 40 feet = 1200 square feet.
Thickness in feet: 4 inches / 12 inches/foot = 0.3333 feet.
Volume in cubic feet: 1200 sq ft * 0.3333 ft = 400 cubic feet.
Volume in cubic yards: 400 cubic feet / 27 cubic feet/yard = 14.81 cubic yards.
Therefore, you will need approximately 14.81 cubic yards of concrete for a 30x40 slab, 4 inches thick. It is highly recommended to order slightly more concrete, typically between 15.5 to 16 cubic yards, to account for potential inaccuracies in the sub-base, spillage, and other variables.
Given this significant volume, purchasing concrete in individual bags is completely unfeasible. A project of this scale absolutely necessitates ordering ready-mix concrete from a specialized supplier. Professional concrete patio contractors are essential for its proper execution.
Detailed Concrete Volume Calculation
Understanding the precise steps to calculate concrete volume is fundamental. This ensures accurate ordering and helps avoid costly overages or shortages. For a 30x40 slab, even small miscalculations can lead to large discrepancies in material.
Step 1: Calculate the Area
The first step is to determine the total surface area of your slab. This is a straightforward multiplication of length by width.
Length: 40 feet
Width: 30 feet
Area = 40 ft * 30 ft = 1200 square feet.
To put this in perspective, 1200 square feet is equivalent to a very large three-car garage. It provides an expansive space for numerous applications.
Step 2: Convert Thickness to Feet
Concrete thickness is usually given in inches, but volume calculations require consistent units (feet).
Thickness: 4 inches
Conversion: 4 inches / 12 inches per foot = 0.3333 feet.
This conversion factor is critical for accurate volume determination. Even slight errors here can compound for a large slab.
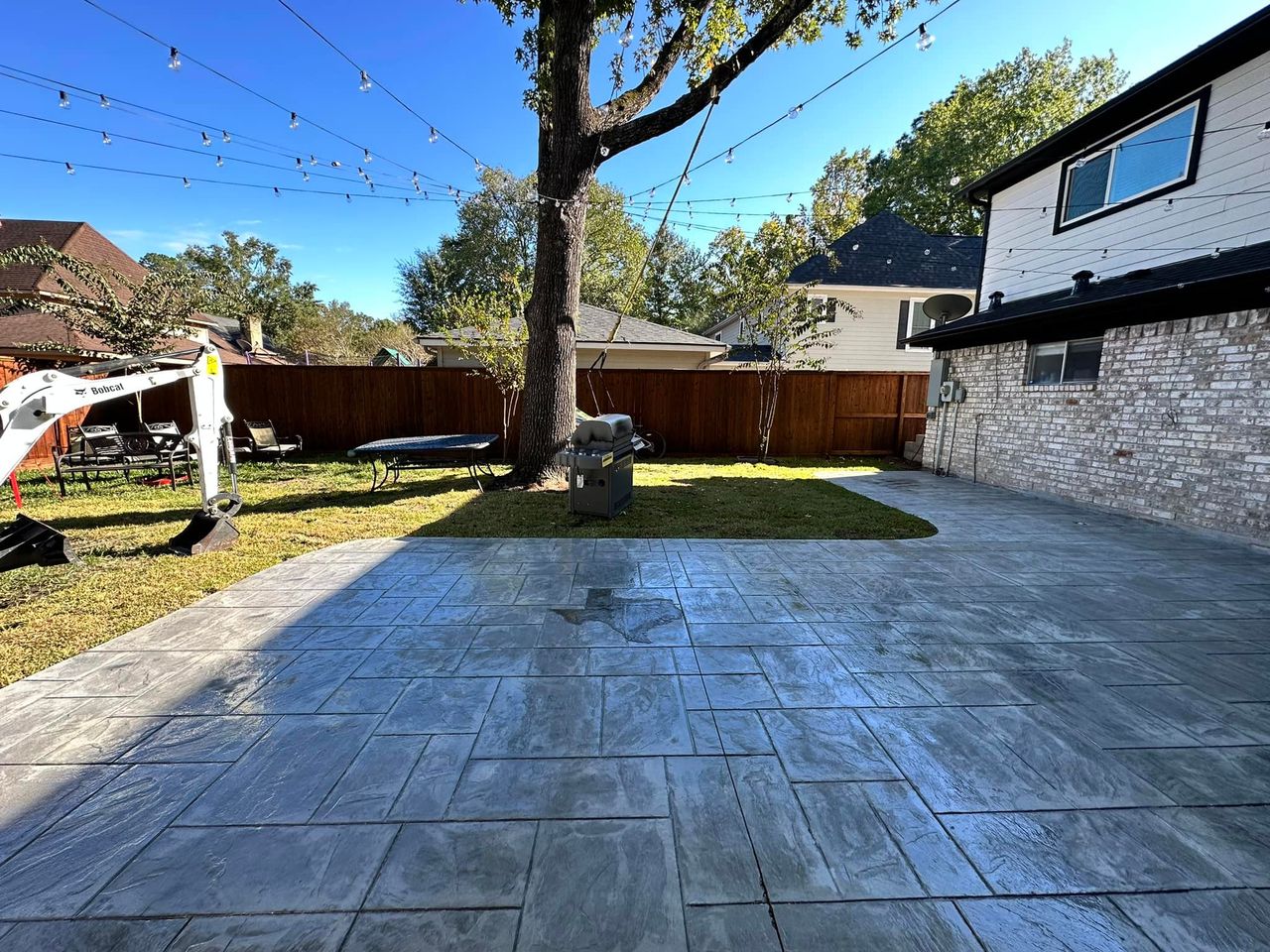
Step 3: Calculate Volume in Cubic Feet
Now, multiply the area by the thickness in feet to get the volume in cubic feet.
Volume = Area * Thickness (in feet)
Volume = 1200 sq ft * 0.3333 ft = 400 cubic feet.
This intermediate step represents the total space your concrete will occupy. It highlights the vast quantity of material.
Step 4: Convert to Cubic Yards
Concrete is sold by the cubic yard, which is the standard unit for bulk orders. There are 27 cubic feet in one cubic yard.
Volume in Cubic Yards = Volume in Cubic Feet / 27
Volume = 400 cubic feet / 27 cubic feet/yard = 14.81 cubic yards.
This final calculation gives you the exact amount of ready-mix concrete to order. It's the most crucial number for your material procurement.
Ordering a Buffer
It is always prudent to order slightly more concrete than the exact calculated volume.
Recommended Overestimation: Add an extra 0.5 to 1 full cubic yard to your order. For 14.81 cubic yards, consider ordering 15.5 to 16 cubic yards.
Reasons for Buffer: This accounts for minor inconsistencies in the sub-base depth, spillage during the pour, and any slight variations in measurement.
Preventing Shortages: Running short of concrete during a large pour is a major problem. It can lead to unsightly and structurally weak "cold joints" if new concrete isn't added before the previous batch sets.
A small overestimation is a wise investment to ensure a continuous and high-quality pour.
Why Ready-Mix Concrete is the ONLY Option for a 30x40 Slab
For a slab requiring nearly 15 cubic yards of concrete, there is simply no practical alternative to ready-mix concrete. Attempting to use individual bags for a project of this scale is not merely difficult; it's virtually impossible to achieve a quality result.
Impossibility of Bagged Concrete
Let's illustrate why using bags is out of the question for a 30x40 slab:
Bag Count Calculation: To yield 400 cubic feet of concrete:
If using 80-pound bags (approx. 0.6 cu ft/bag): 400 / 0.6 = 667 bags.
If using 60-pound bags (approx. 0.45 cu ft/bag): 400 / 0.45 = 889 bags.
Logistics Nightmare:
Storage: Where would you store 600-900 bags of concrete mix? They are heavy and take up immense space.
Transportation: Getting that many bags to your site would require multiple trips with a heavy-duty truck or trailer.
Disposal: You would be left with hundreds of empty, dusty plastic or paper bags to dispose of, incurring significant waste management costs.
Labor & Time:
Physical Impossibility: Lifting, cutting, and mixing 600-900 bags manually is an unimaginable task. It's physically exhausting and prone to injury.
Time Constraints: Concrete begins to set quickly. Mixing hundreds of bags one by one, then wheelbarrowing the concrete across 1200 sq ft, would take days. It's impossible to maintain a continuous pour.
Cold Joints: This sequential mixing would lead to severe "cold joints." These are weak, visible lines where fresh concrete meets concrete that has already begun to harden. Cold joints compromise the entire slab's strength and appearance.
Consistency: Achieving a consistent water-to-cement ratio and slump (consistency) for hundreds of individual batches is impossible. This results in wide variations in strength, color, and finish across the slab, making it unsightly and prone to uneven wear.
Cost: The cost per cubic yard of bagged concrete is dramatically higher than bulk ready-mix. The material cost alone for 15 cubic yards of bagged concrete would be astronomical, often multiple times the cost of ready-mix.
The scale of a 30x40 slab fundamentally rules out the use of bagged concrete. It's not a viable or advisable approach.
Overwhelming Advantages of Ready-Mix
Ready-mix concrete is precisely formulated and delivered to your site in specialized trucks. It is the gold standard for projects of this size for numerous reasons:
Volume & Speed: A ready-mix truck delivers the entire quantity of concrete at once. This allows your crew to place the concrete continuously and rapidly.
Consistency & Quality Control: Concrete plants use automated systems to precisely proportion cement, aggregates, water, and admixtures. This ensures uniform strength (PSI), slump, and quality throughout the entire batch. You eliminate batch-to-batch inconsistencies.
Labor Efficiency: Ready-mix dramatically reduces the labor required for mixing. Your crew can focus entirely on the critical tasks of placing, screeding, floating, and finishing the concrete within the limited working time.
Reliability: You get a high-quality, homogeneous product that meets specified engineering standards. This ensures a cohesive, strong, and durable slab that will last for decades.
For a 1200 sq ft slab, ready-mix concrete is not just convenient; it is an absolute necessity for achieving a professional and long-lasting result.
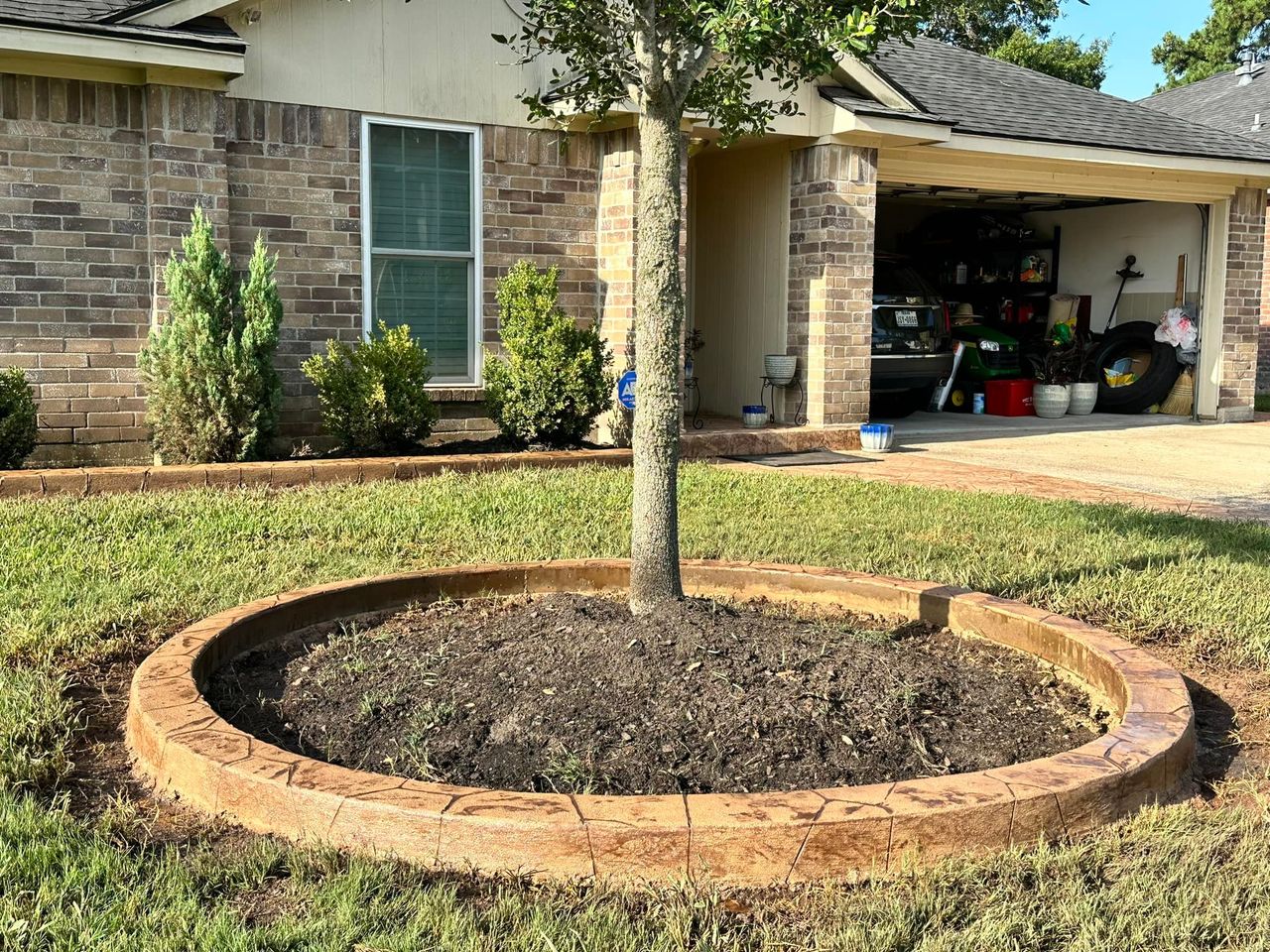
Ordering Ready-Mix for a Large Slab
Placing an order for such a large volume of ready-mix requires specific information and coordination:
Key Specifications:
Cubic Yards: Be precise with your calculated volume (e.g., 14.81 + buffer, so 15.5 or 16 cubic yards).
PSI (Pounds per Square Inch): For a 4-inch patio slab, 2500-3000 PSI concrete is typical. For higher strength or potential vehicle loads, 3500-4000 PSI may be specified.
Slump: This is a measure of the concrete's consistency (how wet it is). Your concrete contractor will advise the optimal slump for your project's workability and desired finish.
Admixtures: Discuss adding fibers (for crack control, especially crucial for large slabs), water reducers (to improve workability without adding water), or air-entrainment (for freeze-thaw resistance, less critical in Houston but still a durability enhancement).
Scheduling: This is critical. Coordinate the concrete delivery time precisely with your crew's readiness. There's a limited window to work the concrete. Ensure the site is fully prepared, forms are set, and all tools are ready.
Site Access: Inform the ready-mix company about the accessibility of your site for their large trucks. Note any tight turns, overhead wires, or soft ground. This helps them plan their approach.
Payment Terms: Understand the company's payment policy. Many require a deposit and balance upon delivery or completion.
Clear and accurate communication with your ready-mix supplier is vital for a smooth and successful pour.
Essential Logistics and Equipment for a 1200 sq ft Pour
Pouring a 30x40 foot concrete slab is a large-scale operation that demands specialized logistics and heavy-duty equipment. This is far beyond the scope of typical homeowner tools.
Concrete Pump (Almost Certain Requirement)
For 14.81 cubic yards spread over 1200 sq ft, a concrete pump is almost always a necessity, even if the ready-mix truck can get relatively close.
Why Needed: Pumps allow for rapid, controlled, and precise placement of large volumes of concrete. They can reach areas inaccessible to the truck's chute, and their speed is critical for preventing cold joints on such a large slab.
Types:
Line Pumps: Smaller, often towed, and use flexible hoses to deliver concrete. Suitable for moderate volumes and reaching awkward spots.
Boom Pumps: Large truck-mounted pumps with an extendable hydraulic arm (boom). They can reach over houses or other obstacles and deliver very high volumes of concrete quickly. For a 30x40 slab, a boom pump is often preferred for its efficiency.
Cost: Renting a concrete pump (which includes an experienced operator) is a significant additional expense, typically ranging from $600 to $1,500+ for a minimum service period. Despite the cost, it's an investment that ensures a successful, high-quality large pour.
The efficiency a pump provides on a project of this scale is invaluable.
Adequate Manpower
A 1200 sq ft concrete pour requires a large, highly coordinated, and experienced crew.
Crew Size: Expect a minimum of 6-10 people or more, depending on the complexity of the pour and the desired finish.
Roles: Crew members have specialized roles:
Spreaders: Guide the concrete as it comes out of the chute/pump hose.
Screeders: Level the concrete to the proper grade.
Floaters/Trowel Operators: Work the surface to achieve the desired finish.
Edgers/Groovers: Create clean edges and control joints.
Pump Operator Liaison: Communicates with the pump operator.
The speed at which a large volume of concrete sets demands immediate, skilled attention from a full team.
Specialized Tools
Professional-grade tools are essential for efficiently handling and finishing such a large concrete area.
Power Screeds: Long, vibrating tools that sit on top of the forms. They are vital for quickly leveling large spans of concrete. Manual screeding for 40 feet would be incredibly arduous and slow.
Power Trowels: Walk-behind or ride-on machines with rotating blades used for efficient, large-area finishing to achieve smooth or hard troweled surfaces. Essential for a 1200 sq ft slab.
Large Bull Floats: Long-handled floats used for the initial smoothing of the concrete surface after screeding.
Laser Levels: Provide pinpoint accuracy for establishing grade and elevation across the entire slab.
Hand Tools: A full array of hand floats, trowels, edgers, groovers, and shovels for detailed work.
Water Supply: A readily accessible water source and hose are needed for cleanup, and potentially for wet curing methods.
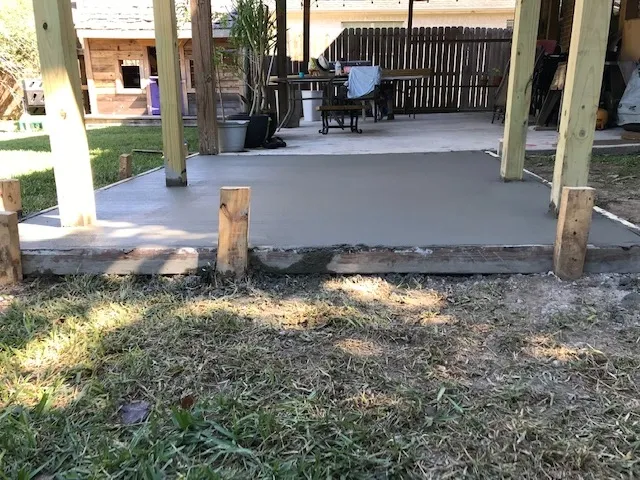
These tools, combined with a skilled crew, are what distinguish a professional concrete pour from an amateur attempt.
Comprehensive Site Preparation for a 30x40 Slab
Proper site preparation is the most critical phase of any concrete project, especially for a large 30x40 foot slab. Its quality directly determines the slab's stability, longevity, and resistance to cracking. For properties in Houston, Texas, specific considerations for expansive clay soils become even more paramount.
1. Clearing and Demolition
Thorough Removal: All existing vegetation, tree roots, old paving (asphalt, existing concrete), debris, and any old structures must be completely removed from the 1200 sq ft area. This creates a clean and stable base.
Professional Demolition: For a slab of this size, demolition often requires heavy equipment (e.g., skid-steer loader with a breaker) and professional hauling services. This adds considerable cost.
A clean, obstruction-free site is the starting point for a successful foundation.
2. Excavation and Initial Grading
Precise Depth: The site must be excavated to the correct depth, accommodating both the 4-inch concrete slab and the underlying sub-base (typically 4-6 inches of gravel). So, total excavation might be 8-10 inches deep.
Accurate Slope: For outdoor patios, ensuring proper drainage is vital. The ground must be graded with a consistent slope, typically a minimum of 1/4 inch per linear foot, away from any adjacent structures (like your house). This prevents water from pooling on the surface.
Houston Specific: Addressing Expansive Clay: Houston's expansive clay soils swell significantly when wet and shrink when dry. This movement can put immense stress on a slab.
Over-excavation and Replacement: In some cases, more reactive topsoil may be excavated, and stable engineered fill (such as select granular material) is brought in and compacted in lifts.
Moisture Conditioning: Some contractors use moisture conditioning techniques (pre-wetting the subgrade) to stabilize the clay before placing the sub-base.
Proper excavation and initial grading lay the groundwork for a stable, well-draining slab.
3. Sub-Base Installation and Compaction
A well-constructed sub-base is essential for distributing the slab's load evenly and promoting drainage.
Material & Depth: A minimum of 4 to 6 inches of granular material (like crushed stone or gravel, free of fines) is spread over the excavated and compacted native soil. For a 1200 sq ft area, this requires a large quantity of aggregate.
Layering and Compaction: The sub-base material should be spread in uniform lifts (layers) of no more than 4 inches. Each lift must be thoroughly compacted using a heavy vibratory plate compactor or a small roller. This densifies the material and prevents future settling.
Moisture Barrier (Vapor Barrier): For a large patio, especially in a humid climate like Houston, installing a 6-mil (or thicker) polyethylene vapor barrier over the compacted sub-base is highly recommended. It prevents moisture from migrating up from the ground into the concrete, which can cause efflorescence (white mineral deposits) and other moisture-related issues.
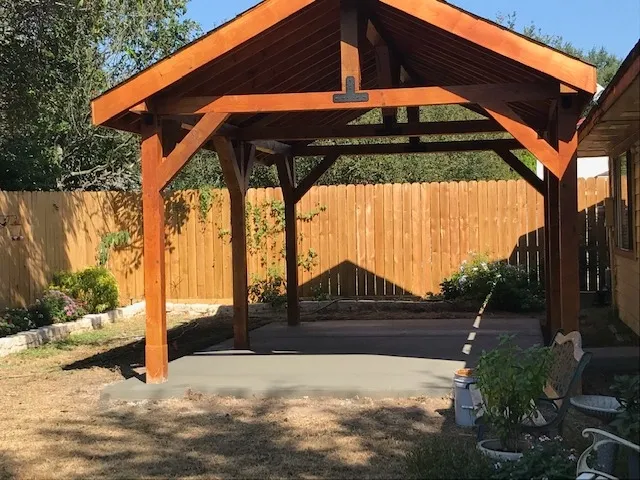
The sub-base is the true foundation of your concrete slab, significantly impacting its performance.
4. Formwork Construction
Forms define the exact perimeter and height of your concrete slab. For a 30x40 slab, this involves 140 linear feet of formwork.
Scale: The forms must be built accurately to the precise dimensions.
Sturdiness: They must be extremely sturdy and well-braced to withstand the immense outward pressure from nearly 15 cubic yards of wet concrete.
Accuracy: Forms must be perfectly level (or sloped as per drainage plan) and square. Any misalignment will result in an uneven or improperly shaped slab.
Precise and robust formwork is critical for a well-defined and uniformly thick slab.
5. Reinforcement Installation
Reinforcement is vital for controlling cracking and enhancing the structural integrity of a large concrete slab.
Wire Mesh vs. Rebar: While wire mesh (e.g., 6x6-10/10) is often used for smaller, lighter-duty slabs, for a 1200 sq ft slab, steel rebar (reinforcing bar) is highly recommended for superior structural strength and crack control. A common pattern is #3 or #4 rebar placed in a grid pattern (e.g., 18-24 inches on center).
Proper Placement: Reinforcement must be correctly positioned within the concrete. It should be elevated to the middle or lower third of the slab's thickness using "chairs" or concrete bricks. If reinforcement lies directly on the sub-base, it's ineffective.
Properly installed reinforcement is a key defense against future cracking.
6. Drainage Planning
Given Houston's climate, meticulous drainage planning is crucial for a 1200 sq ft patio.
Surface Slope: Reiterate that the slab itself must have a consistent slope (1/4 inch per foot minimum) away from the house and other structures.
Trench Drains/Catch Basins: For such a large area, trench drains along the edges or strategically placed catch basins are often necessary to efficiently collect and divert large volumes of rainwater.
Routing Water Away: Ensure that all collected water is routed via pipes far away from the slab, your house foundation, and neighboring properties.
Comprehensive drainage prevents water damage and preserves the slab's sub-base.
The Concrete Pour and Finishing Process
The actual concrete pour is a rapid and highly coordinated event for a 30x40 slab. The setting time of concrete demands immediate, skilled attention from a large crew.
Pre-Pour Checklist
Before the ready-mix truck or pump arrives, a meticulous final inspection is critical.
Forms: Confirm forms are perfectly level (or sloped), square, and securely braced.
Sub-Base: Ensure the sub-base is thoroughly compacted, moist (but not saturated), and free of debris.
Reinforcement: Verify that all reinforcement (rebar, mesh) is properly laid out and elevated using chairs.
Tools Ready: All necessary hand tools, power tools (screeds, trowels), wheelbarrows, and water hoses must be clean and readily accessible.
Crew Briefing: Ensure every crew member understands their role and the pouring sequence.
A thorough checklist minimizes potential delays and costly errors during the pour.
The Pour
This is the most time-sensitive phase, requiring rapid action.
Controlled Discharge: The ready-mix truck (or pump) discharges concrete in a controlled manner into the forms.
Spreading: Crew members with shovels and rakes quickly spread the concrete evenly across the entire 1200 sq ft area.
Vibration (if needed): For thicker or heavily reinforced slabs, concrete vibrators may be used to remove air pockets and ensure dense concrete around rebar.
Speed and coordination are paramount to ensure the concrete is placed before it begins to stiffen.
Screeding
Leveling: Immediately after spreading, the concrete is "screeded" or struck off. A long straightedge (often a power screed for a 30x40 slab) is used to level the concrete to the top of the forms.
Removing Excess: Screeding removes any excess concrete and establishes the precise slab elevation and slope.
Precise screeding is crucial for achieving a uniform thickness and desired grade.
Floating and Troweling
These steps densify the concrete surface and bring a smooth, workable "cream" to the top.
Floating (Initial): A bull float or hand float is used to smooth the surface, embed any larger aggregates, and prepare the surface for final finishing.
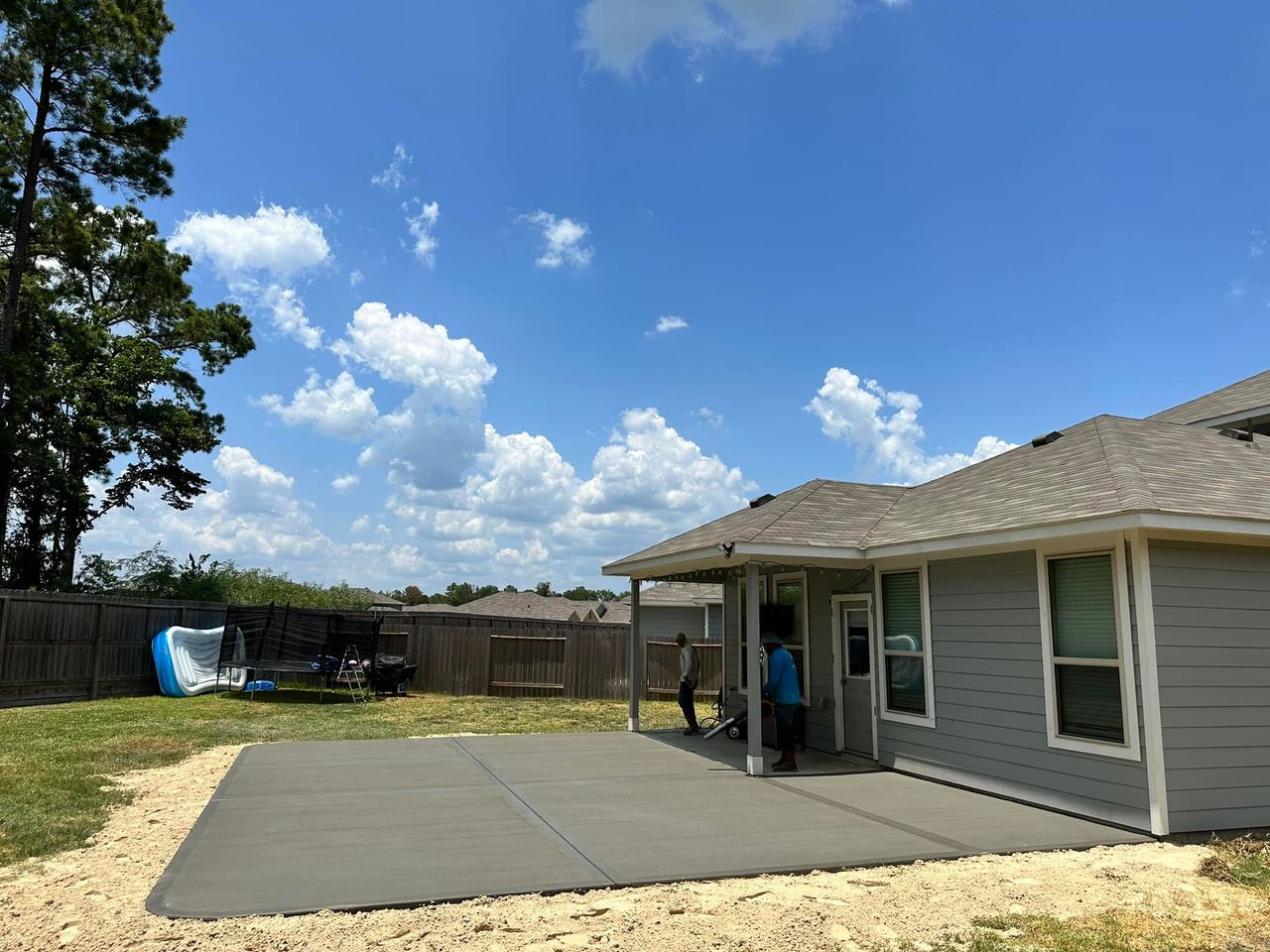
Troweling (Final): As the concrete stiffens, hand trowels or, more commonly for a 1200 sq ft slab, walk-behind or ride-on power trowels are used. Multiple passes achieve the desired surface smoothness and density (e.g., broom finish for slip resistance, smooth trowel for garage floors).
Timing: The timing of these finishing steps is critical, requiring experienced judgment of the concrete's setting progress.
Skilled finishers are essential for achieving a durable and aesthetically pleasing surface.
Edging and Control/Expansion Joints
These are crucial for managing concrete's natural tendency to crack.
Edging: A concrete edger is used along all perimeter edges to create a smooth, rounded finish. This prevents chipping and provides a clean, professional look.
Control Joints: For a 1200 sq ft slab, control joints (grooves or saw cuts) are absolutely critical. They are strategically placed to create weakened planes. These encourage any shrinkage cracks to form neatly along the joints, rather than randomly across the slab. For a 30x40 slab, joints should typically be spaced no more than 10-15 feet apart in any direction, forming a grid.
Expansion Joints: Full-depth joints are placed where the concrete slab meets other fixed structures (e.g., house foundation, existing driveway, columns). These allow the slab to expand and contract independently, preventing stress cracks caused by thermal movement.
Proper joint placement is a fundamental aspect of crack control and long-term slab integrity.
Curing
This is arguably the most vital step after the pour for achieving the concrete's designed strength and durability.
Process: Concrete needs to remain moist for a specific period (typically 3-7 days for initial cure, 28 days for full strength development). This allows the cement to fully hydrate.
Methods: Common curing methods include continuous misting, covering the slab with plastic sheeting or wet burlap, or applying a liquid curing compound.
Importance: Skipping or rushing the curing process can significantly reduce the concrete's strength, increase its susceptibility to cracking, dusting, and spalling, and compromise its long-term performance.
Proper curing is a low-cost step that yields massive benefits for the slab's lifespan.
Sealing
Protection: After the concrete has fully cured (typically after 28 days), applying a high-quality concrete sealer is highly recommended. Sealers penetrate the concrete surface and protect it from moisture penetration, stains, abrasion, and UV damage.
Maintenance: Sealers need reapplication every 2-5 years, depending on product type and traffic.
Sealing extends the patio's life and maintains its aesthetic appeal.
Cost Considerations for a 30x40 Concrete Slab (4 Inches Thick)
The cost of a 30x40 concrete slab is a significant investment. Understanding the various components that contribute to the total price is essential for accurate budgeting. For a 4-inch thick slab, the primary costs will be materials, labor, and equipment.
Material Costs
Concrete: The largest material expense. For 15-16 cubic yards, expect to pay approximately $1,800 to $2,900+ for the ready-mix concrete itself, including standard delivery fees (prices vary by region and supplier).
Sub-Base Aggregates: For a 1200 sq ft slab requiring 4-6 inches of gravel, this will be a substantial volume (e.g., 18-27 cubic yards of gravel). Cost for material and delivery can be $500 to $1,500+.
Reinforcement:
Wire mesh is less expensive, perhaps $200-$400.
Rebar for 1200 sq ft would be significantly more, ranging from $600 to $1,200+ depending on rebar size and spacing.
Formwork Materials: Lumber, stakes, screws. Cost typically $200-$500.
Vapor Barrier (if used): A few hundred dollars for the material.
These material costs combined can easily total $2,700 to $6,100+.
Labor Costs
Labor is often the largest single component, typically accounting for 50-70% of the total project cost.
For a 1200 sq ft slab, a large, experienced crew is needed for several days (site prep, forming, pouring, finishing, curing oversight).
Expect labor costs to range from $3,000 to $10,000+, depending on local rates in Houston, crew size, and complexity of finish.
Equipment Rental/Use
Concrete Pump: As discussed, often a flat fee of $600 - $1,500+.
Heavy Equipment (for site prep): Skid-steer or mini-excavator rental for demolition, excavation, and moving aggregates, often with operator. This can be $500-$1,500+ per day.
Compaction Equipment: Plate compactor rental, $100-$200+ per day.
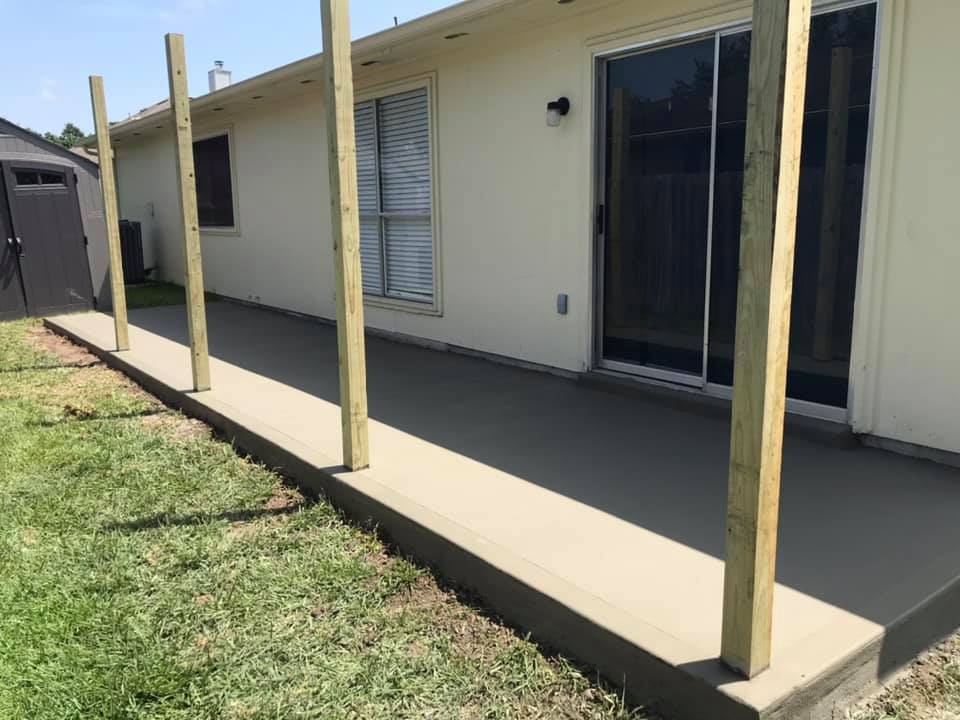
Power Tools: Rental for power screeds and power trowels, $100-$300+ per day for each.
These equipment costs are substantial and often necessitate hiring a professional.
Site Preparation Costs
Excavation and Grading: Labor and equipment for moving earth.
Demolition and Hauling: If an existing structure needs removal, this can add $2-$6 per sq ft, so $2,400 to $7,200+ for 1200 sq ft.
Dirt Disposal: If excess dirt needs to be hauled away, this incurs additional fees.
Site preparation can be one of the most variable and costly components.
Permits
For a large 1200 sq ft concrete slab, particularly if it's for a garage or structure, permits from the City of Houston or relevant county are likely required. Permit fees vary but are a necessary expense, often handled by the contractor.
Total Project Range
Considering all these factors, the total cost for a 30x40 slab (4 inches thick) can range significantly.
A basic slab with a broom finish might start from $5 to $8 per square foot, totaling $6,000 to $9,600.
With more extensive site preparation, rebar reinforcement, and a higher-quality finish (like stamped or colored concrete), the cost can easily rise to $10 to $15+ per square foot, totaling $12,000 to $18,000 or more.
A 30x40 concrete slab is a large construction investment.
Why Professional Concrete Patio Contractors are Essential
The sheer scale and complexity of pouring a 30x40 concrete slab make professional concrete patio contractors not just advisable, but absolutely essential. This is a project that virtually guarantees failure for an inexperienced DIYer.
Complexity of Scale
A 1200 sq ft concrete slab is a major undertaking. It involves large volumes of material, demanding logistics, and precise execution within tight timeframes.
Rapid Setting: Concrete sets quickly. A large slab requires simultaneous, coordinated effort from a skilled team to spread, screed, float, and finish the entire area before it hardens.
Logistics Management: Coordinating ready-mix delivery, concrete pump operation, and the movement of a large crew and heavy equipment is complex.
This is a job for experienced professionals.
Expertise in Local Conditions
Houston's Expansive Clay: Concrete contractors familiar with Houston, Texas, deeply understand its challenging expansive clay soils. They know the correct methods for sub-base preparation, reinforcement, and drainage to mitigate soil movement and prevent future cracking or heaving of the slab.
Climate Challenges: They account for local weather patterns, especially heavy rainfall, in their planning and execution to ensure proper curing and drainage.
Local expertise is invaluable for long-term durability.
Access to Equipment & Manpower
Professional contractors own or have ready access to the heavy machinery required: excavators, plate compactors, power screeds, power trowels, and concrete pumps. Renting all these individually is expensive and complex.
They have a trained and experienced crew large enough to handle the rapid pace of a large concrete pour efficiently and effectively.
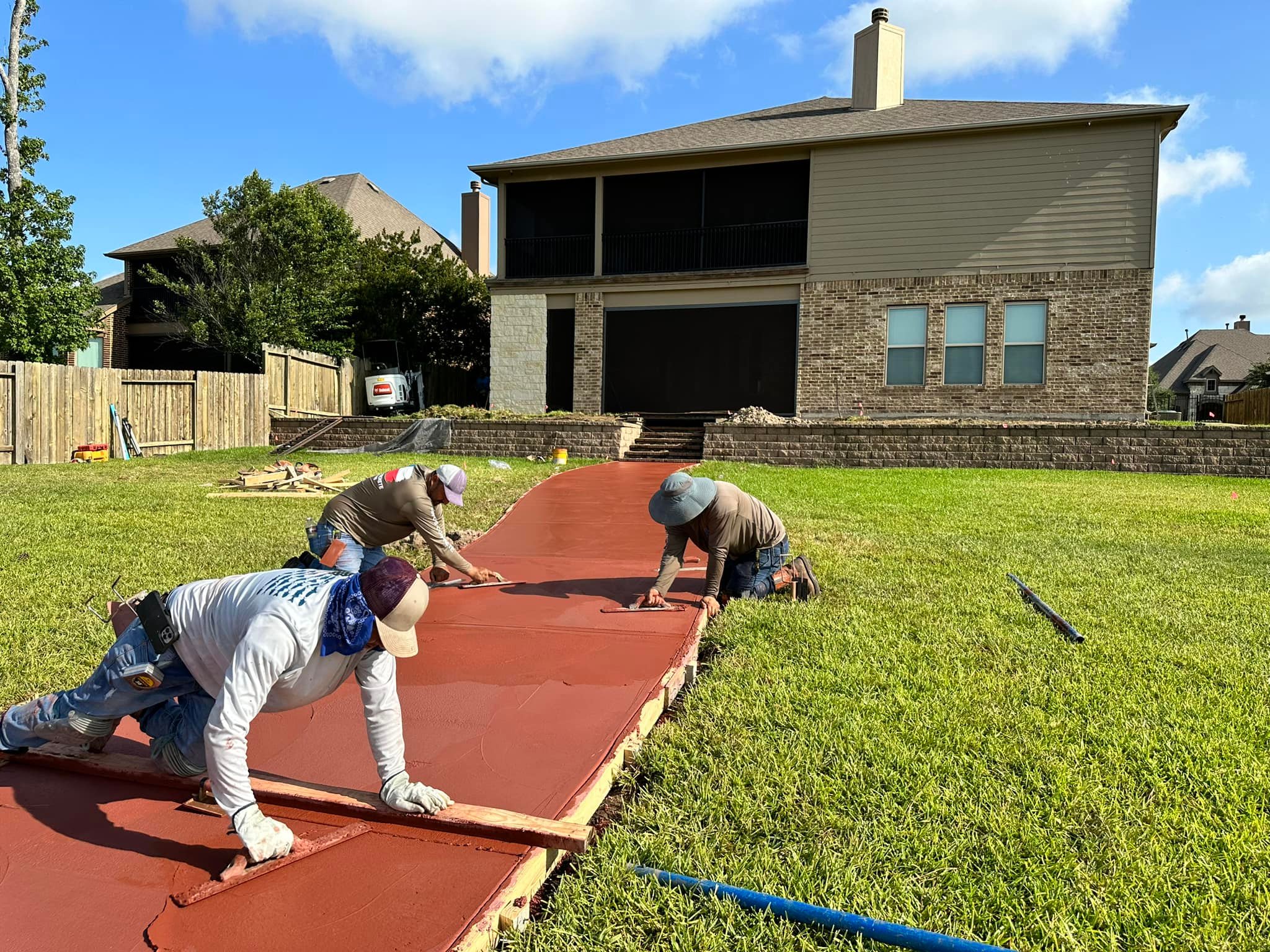
Attempting this project without the right equipment and sufficient manpower is a recipe for disaster.
Quality Assurance & Warranty
A professional contractor ensures a high-quality finished product. They guarantee proper concrete mix, correct installation techniques, and appropriate finishing.
Reputable concrete patio contractors provide a warranty on their workmanship. This gives you peace of mind, knowing your significant investment is protected.
A professional result adds significant value and longevity to your property.
Navigating Permits & Codes
For a large 30x40 slab, especially if it's for a garage or a covered structure, permits from local authorities (City of Houston or county) are highly likely to be required.
Professional contractors are familiar with local building codes and handle the entire permitting and inspection process. This ensures your project is compliant and avoids potential legal issues or fines.
Finding the Right Professional (Houston, TX)
When searching for "concrete patio contractors near me" for a large project like a 30x40 slab in Houston:
Verify Licensing and Insurance: Always ensure the contractor is properly licensed and carries comprehensive liability and worker's compensation insurance.
Experience with Large Slabs: Ask specifically about their experience with concrete pours of similar size (1000+ sq ft). Request references and view their portfolio of previous work.
Detailed Quotes: Obtain at least three written, itemized quotes that specify all costs for materials, labor, equipment, and any site-specific challenges.
Local Reputation: Check online reviews and ask for local client references.
Communication: Choose a contractor who communicates clearly, responds promptly, and is transparent about the process.
In the Houston area, Cincos Concrete LLC is a local concrete company experienced in handling large-scale concrete slab installations, from initial site preparation to final finishing. They possess the expertise necessary for a project of this magnitude.
Conclusion
For a 30x40 concrete slab, 4 inches thick, you will need approximately 14.81 cubic yards of concrete. It is advisable to order 15.5 to 16 cubic yards to ensure sufficient material for the entire pour.
Crucially, for a slab of this size (1200 sq ft), ready-mix concrete is the only viable option. The logistical challenges, labor intensity, and quality control issues associated with using hundreds of individual bags of concrete make it impractical and virtually impossible to achieve a professional result.
Successfully installing such a large concrete slab demands extensive site preparation, specialized heavy equipment (including a concrete pump), and a large, experienced crew. The process from excavation, sub-base installation, forming, reinforcement, to the rapid pour and precise finishing requires professional expertise.
Therefore, engaging professional concrete patio contractors is essential for a project of this magnitude. Their knowledge of local conditions (like Houston's expansive clay soils), access to necessary equipment, skilled manpower, and understanding of permitting and building codes will ensure your 30x40 slab is installed correctly, durably, and efficiently. Investing in professional installation is the best way to guarantee a long-lasting and valuable addition to your property.