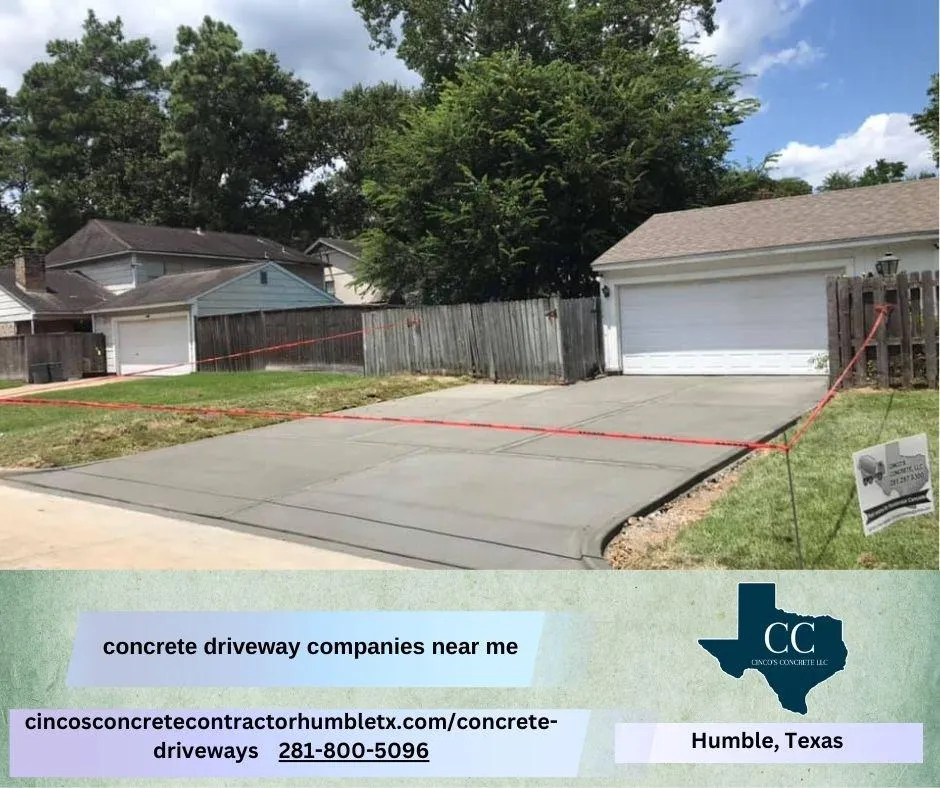
How Much Is a 10 Yard Truck of Concrete?
How Much Is a 10 Yard Truck of Concrete?
When embarking on a significant concrete project, such as a large patio, a garage slab, or a substantial portion of a concrete driveway, ordering ready-mix concrete by the truckload becomes the most practical and often most economical option. Understanding the cost of a 10-yard truck of concrete is crucial for accurate budgeting. This quantity represents a substantial volume, capable of covering considerable ground.
The price of ready-mix concrete is not static. It fluctuates based on numerous variables. These factors range from regional market conditions to the specific mix design required for your project. Labor, fuel costs, and even the time of year can influence the final price.
This article will delve into the typical cost range for a 10-yard concrete truck. We will explore the various elements that affect pricing. We will also discuss how to ensure you get the best value for your investment. This knowledge will empower you to plan your concrete project effectively.
Understanding Concrete Pricing Factors
A 10-yard truck of concrete represents a significant quantity of material. Understanding its cost is essential for any substantial construction or home improvement project. This includes foundational slabs or extensive concrete driveway installations. The price can vary considerably based on several influencing factors.
Generally, the cost of a 10-yard truck of standard concrete in mid-2025 can range from $1,100 to $1,800. This figure includes the material itself. It also typically accounts for standard delivery within a certain radius. However, this is a broad estimate.
What is a Cubic Yard of Concrete?
Before diving into truckload costs, it's vital to understand the unit of measurement. Concrete is sold by the cubic yard. One cubic yard is a volume equal to a cube that is 3 feet long, 3 feet wide, and 3 feet high.
This equates to 27 cubic feet. A 10-yard truck, therefore, carries 270 cubic feet of concrete. This volume can cover a significant area, depending on the desired slab thickness.
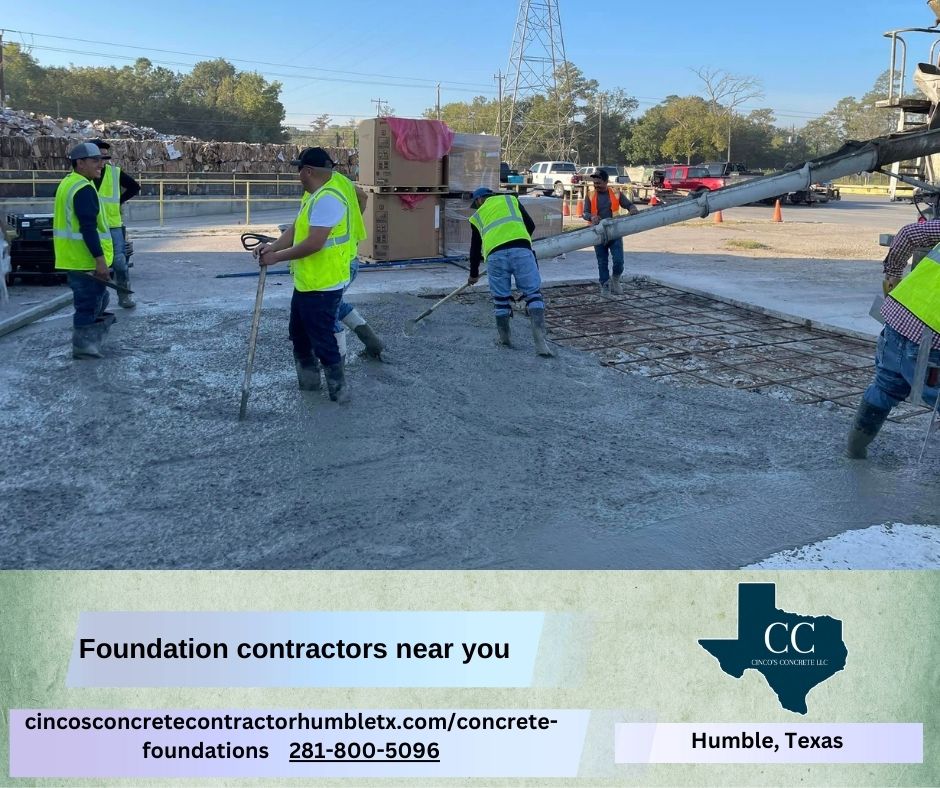
For example, 1 cubic yard will cover 81 square feet at 4 inches thick. A 10-yard truck could cover 810 square feet at that same thickness. This helps visualize the scale of the delivery.
Understanding Concrete Pricing Factors
The price you pay for a 10-yard truck of concrete is influenced by a complex interplay of factors. Being aware of these elements helps you anticipate costs and make informed decisions. Each component adds to the final delivered price.
1. Concrete Mix Strength (PSI)
The strength of concrete is measured in pounds per square inch (PSI). Different applications require different PSI ratings. Higher PSI concrete costs more due to the specific cement and aggregate ratios.
2,500 - 3,000 PSI: This is standard for footpaths, patios, or light-duty shed slabs. It's generally the most affordable option. It provides adequate strength for pedestrian traffic.
3,500 - 4,000 PSI: Often used for garage floors, driveways, and foundations. This mix offers increased durability and can handle heavier loads. A concrete driveway typically requires this strength. It costs more per cubic yard than lower PSI mixes.
4,500 PSI and Above: Reserved for heavy-duty commercial applications, industrial floors, or specific structural elements. These high-strength mixes are the most expensive. They incorporate specialized admixtures.
Always specify the required PSI for your project. Over-specifying can lead to unnecessary expense. Under-specifying can result in structural failure.
2. Additives and Admixtures
Concrete mixes can include various additives and admixtures. These are substances added to alter the concrete's properties. They can increase workability, speed up or slow down setting, or improve durability.
Air-entrainment: Improves resistance to freeze-thaw cycles. Essential in colder climates to prevent cracking. This adds a small cost per yard.
Water Reducers: Allow for a more workable mix with less water, increasing strength. Useful for easier pouring.
Retarders: Slow down the setting time in hot weather. This provides more time for finishing.
Accelerators: Speed up setting time in cold weather. Allows for faster project completion.
Fibers: Synthetic or steel fibers can be added to reduce shrinkage cracking. They provide additional tensile strength.
Each additive or admixture contributes to the overall cost per cubic yard. Discussing your specific needs with the supplier helps them formulate the correct mix. This ensures optimal performance for your concrete driveway or slab.
3. Delivery Fees and Location
The distance from the concrete batch plant to your job site significantly impacts the delivery cost. Concrete companies charge based on mileage and fuel surcharges. Being close to a plant can save you money.
Rural or remote locations will incur higher delivery fees. Urban areas might have higher demand but shorter travel distances. Always clarify delivery charges when getting a quote.
Access to the job site also matters. If the truck cannot easily reach the pour location, additional equipment may be needed. This can include a concrete pump, which carries its own separate costs.
4. Short Load Fees
While this article focuses on a 10-yard truck, it's crucial to understand short load fees. Many concrete companies have a minimum order size for ready-mix delivery, often 5-7 cubic yards. If you order less than their minimum, a "short load" fee applies.
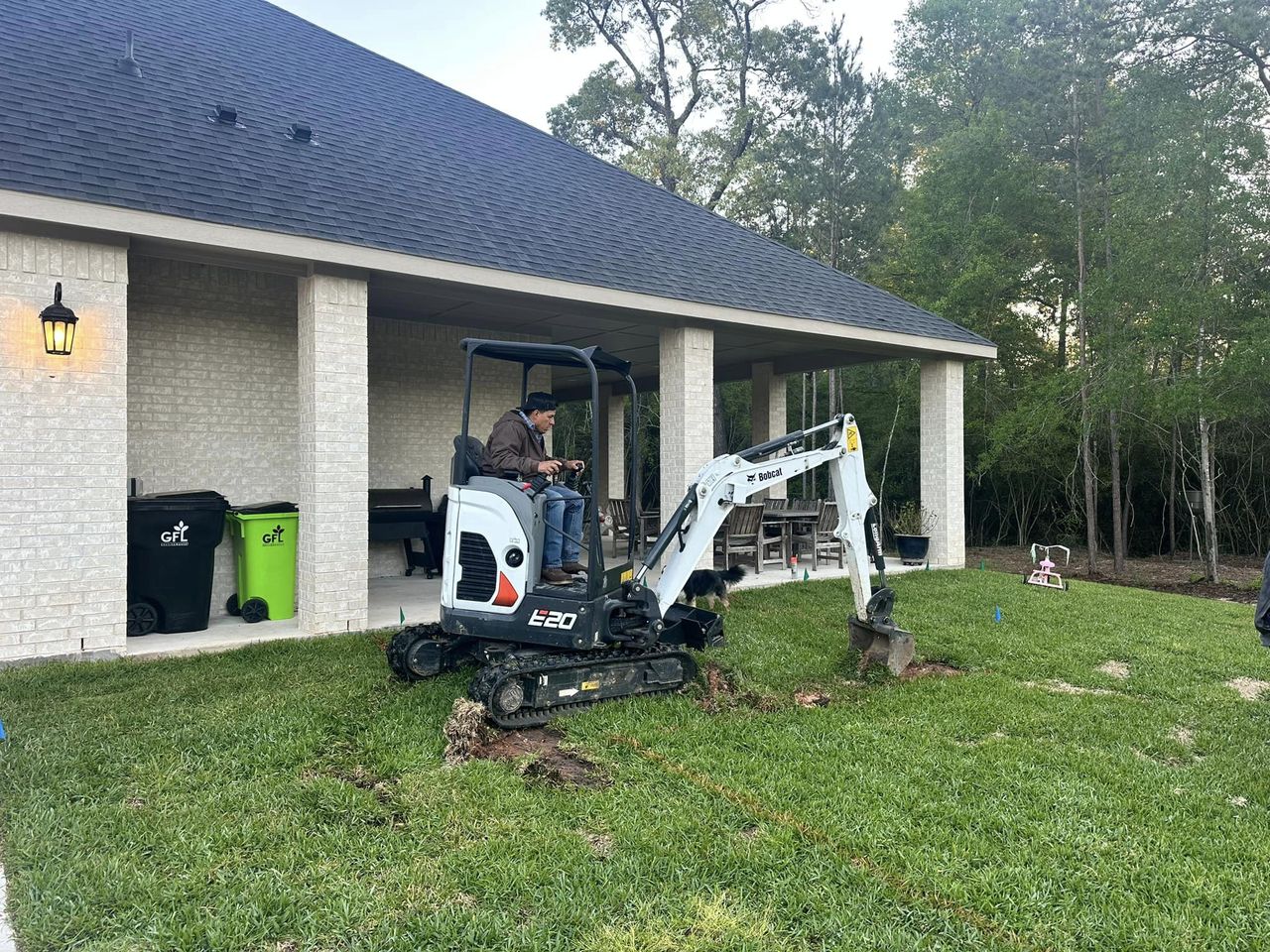
This fee compensates the supplier for the truck's operational costs. These costs include fuel, driver time, and equipment wear. For a 10-yard truck, you're likely exceeding most minimums.
However, if your project size changes last minute, be aware of this potential charge. A full 10-yard load usually avoids these fees. It makes large-scale pouring more cost-efficient per yard.
5. Time of Year and Demand
Concrete prices can fluctuate seasonally. Demand for concrete typically peaks during warmer months. This is when construction activity is highest. Increased demand can lead to higher prices.
Conversely, prices might be slightly lower during off-peak seasons. This includes winter in colder climates. Planning your project during these periods might offer some savings.
Supply and demand dynamics play a role. Regional construction booms can drive up prices. Conversely, a slowdown in building activity might result in more competitive pricing.
6. Fuel Prices
The cost of diesel fuel directly impacts concrete delivery prices. Concrete trucks consume a lot of fuel. Fluctuations in global oil prices can quickly translate to changes in concrete costs.
Suppliers often include a fuel surcharge on their invoices. This surcharge helps them offset rising fuel expenses. It's a variable cost that can shift over time.
Always inquire about current fuel surcharges when requesting a quote. This ensures you have a complete understanding of the potential costs involved.
7. Local Market Conditions and Competition
Concrete prices vary significantly by region and even by city. Local material availability, labor rates, and the number of competing suppliers all play a role. A market with many suppliers may have more competitive pricing.
Areas with limited aggregate quarries or cement plants might see higher prices. Transportation costs for raw materials factor into this. Always get quotes from multiple local suppliers.
This allows you to compare prices. It helps ensure you are getting a fair market rate. Local concrete professionals are best equipped to quote accurate prices.
What a 10-Yard Truck of Concrete Can Cover
Understanding the volume a 10-yard truck delivers is key to planning your project effectively. This amount is substantial and suitable for medium to large-scale pours. It minimizes the need for multiple deliveries.
A cubic yard contains 27 cubic feet. Therefore, a 10-yard truck carries 10×27=270 cubic feet of concrete. This volume can be spread over various areas depending on the required slab thickness.
Standard Slab Thicknesses and Coverage
The most common slab thicknesses for residential and light commercial use are 4, 5, and 6 inches. Each thickness impacts the square footage a 10-yard truck can cover.
4-inch slab: A 4-inch slab is equivalent to 1/3 of a foot (4/12). A 10-yard truck (270 cubic feet) can cover approximately 270 cubic feet/(1/3 ft)=810 square feet. This is suitable for patios, walkways, or shed floors. It's often adequate for lighter-duty concrete driveway sections.
5-inch slab: A 5-inch slab is equivalent to 5/12 of a foot. A 10-yard truck can cover approximately 270 cubic feet/(5/12 ft)=648 square feet. This thickness provides added strength. It is often recommended for garage floors or medium-duty driveways.
6-inch slab: A 6-inch slab is equivalent to 1/2 of a foot (6/12). A 10-yard truck can cover approximately 270 cubic feet/(1/2 ft)=540 square feet. This robust thickness is ideal for heavy-duty driveways. It's also used for parking pads for RVs or commercial applications.
Examples of Projects for a 10-Yard Truck
A 10-yard truck is typically sufficient for:
Standard Two-Car Garage Slab: A typical two-car garage is around 20x20 feet (400 sq ft). At 5 inches thick, this requires approximately 6.2 cubic yards. A 10-yard truck provides ample material, allowing for waste.
Large Patio Area: A patio measuring 25x30 feet (750 sq ft) at 4 inches thick would need about 9.25 cubic yards. A 10-yard truck is perfect for this size.
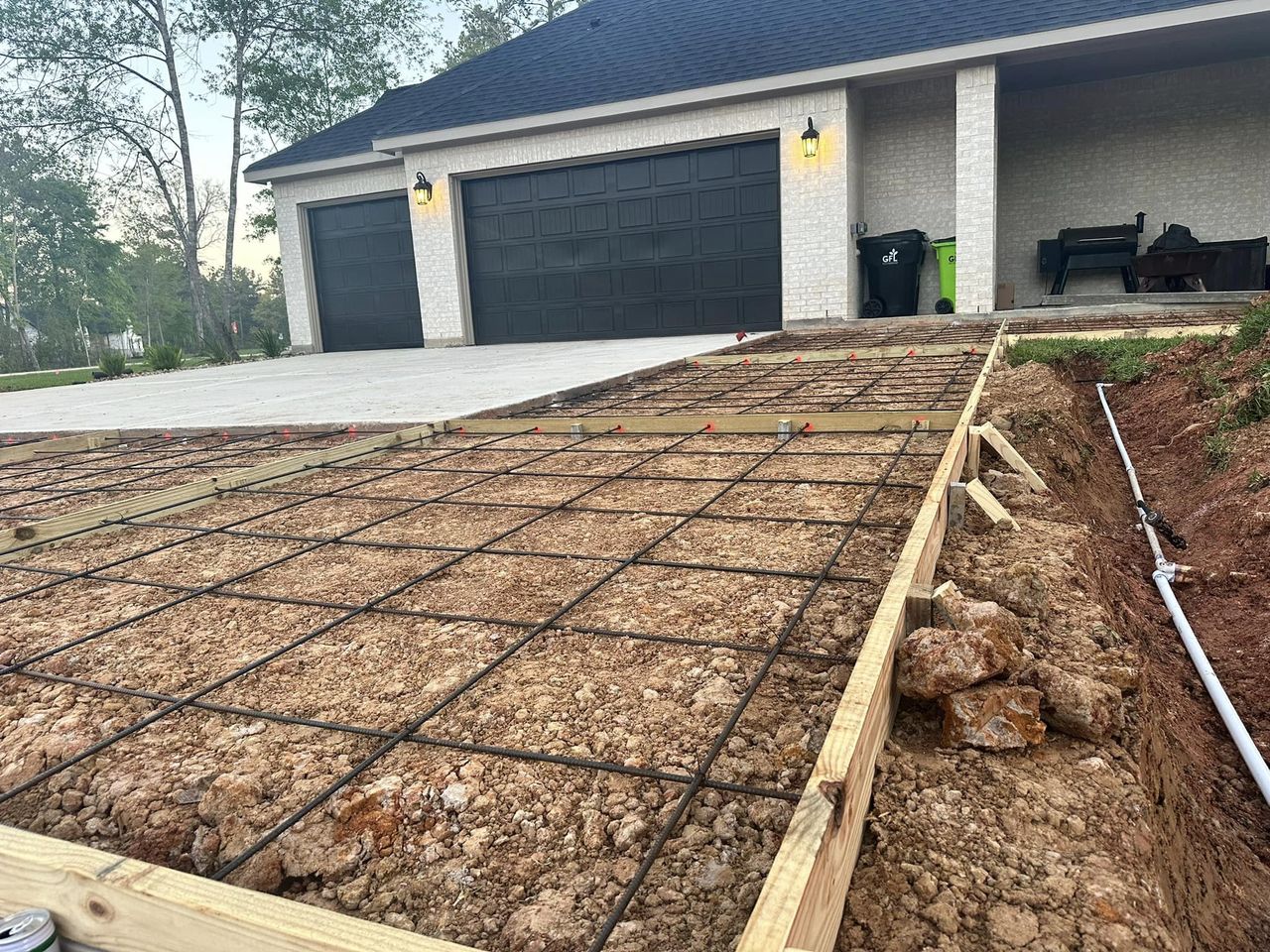
Significant Concrete Driveway Section: If replacing or extending a portion of a concrete driveway, a 10-yard delivery can cover a substantial area. For example, a 30-foot long, 18-foot wide concrete driveway section at 6 inches thick would require 10 cubic yards.
Always measure your project accurately. Calculate the cubic yardage needed. Remember to add a 5-10% waste factor to your calculations. This ensures you order enough concrete.
Ordering and Delivery Process
Ordering ready-mix concrete for a 10-yard truck is a streamlined process. However, careful planning and clear communication with the supplier are essential. This ensures a smooth and efficient delivery.
1. Confirm Your Volume and Mix Design
Before calling, have your exact cubic yardage calculated. This should include your waste factor. Know the required PSI strength. Determine if any admixtures (like air-entrainment) are necessary.
Clearly communicate the purpose of the concrete. Specify if it's for a patio, garage, or a new concrete driveway. This helps the supplier recommend the appropriate mix. Provide accurate dimensions for your project.
2. Get Multiple Quotes
Contact several local concrete suppliers. Request quotes for a 10-yard load of your specific concrete mix. Provide your exact address for accurate delivery fee calculations.
Compare not just the price per yard, but also delivery fees, fuel surcharges, and any potential short-load fees (though unlikely for 10 yards). Ask about minimum order sizes. Inquire about cancellation policies.
3. Schedule the Delivery
Book your concrete delivery well in advance, especially during peak construction season. Specify the exact date and time. Confirm how long the truck can remain on-site without incurring "waiting" or "standby" fees.
Provide clear directions to your site. Discuss any potential access challenges for a large truck. A delivery window is usually provided, so be prepared for arrival within that timeframe.
4. Site Preparation Before Delivery
Ensure your site is fully prepared before the truck arrives. Formwork must be properly set, squared, and braced. Reinforcement (rebar or mesh) should be correctly installed and elevated.
The sub-base should be compacted and level. Ensure adequate access for the concrete truck. Clear any obstacles from the path to the pour location. Have all tools and personnel ready.
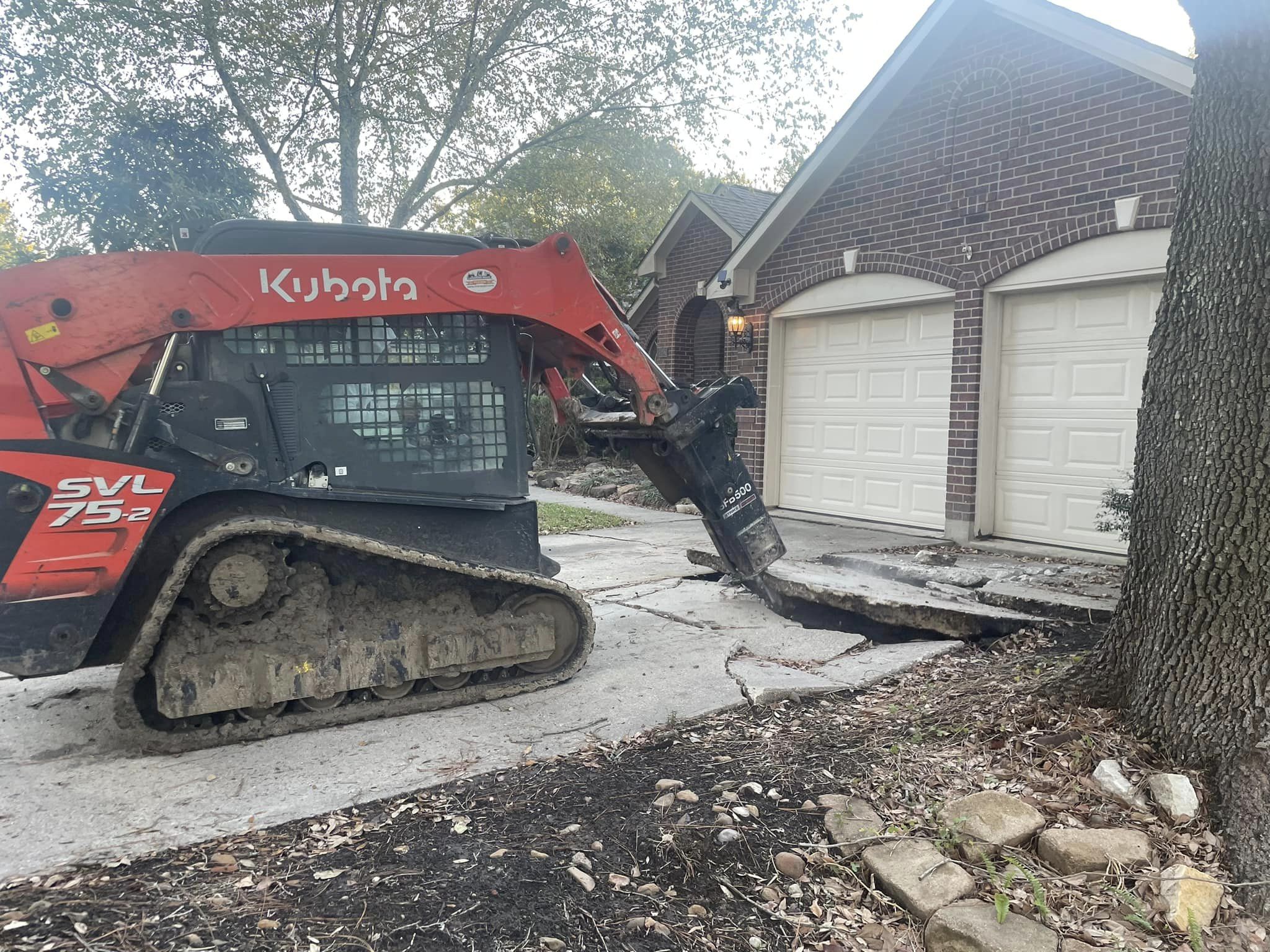
5. Receiving the Concrete
When the truck arrives, guide the driver to the pour location. Be ready to start pouring immediately. Concrete has a limited working time before it begins to set.
Communicate with the driver regarding the slump (consistency) of the concrete. A small amount of water can be added on-site, but excessive water weakens the mix. Use a wheelbarrow or pump for placement if the truck chute cannot reach.
6. Managing the Pour
Have enough personnel on hand to manage a 10-yard pour. This volume is significant. It requires efficient spreading, screeding, and finishing. Timeliness is crucial for a uniform finish.
Direct the truck driver to discharge concrete strategically across the area. Use shovels and rakes to distribute the material. Work quickly to level and smooth the concrete before it becomes too stiff.
7. Post-Delivery Cleanup
Once the concrete is discharged, the truck will need to wash out its drum. Have an designated area for this, often a small pit or contained area on your property. This wash water contains cement and aggregates.
It's important not to allow this wash water to flow into storm drains or natural waterways. Dispose of it responsibly according to local regulations. Proper cleanup is part of a professional concrete job.
Additional Costs Beyond the Concrete Itself
The cost of the concrete truck is a major component, but it's not the only expense for a complete concrete project. Several other factors contribute to the overall budget. These are crucial for a comprehensive financial plan.
1. Site Preparation and Excavation
Before concrete can be poured, the site needs preparation. This includes clearing vegetation, removing existing structures, and excavating to the correct depth. The cost depends on the amount of material to be removed.
If you have an existing concrete driveway to remove, demolition and disposal fees apply. Excavation costs can range from $50 to $200 per cubic yard. This varies based on soil type and accessibility.
Labor for site preparation can be a significant expense. Consider renting equipment like excavators or bobcats for larger jobs. Alternatively, hire a professional excavation service.
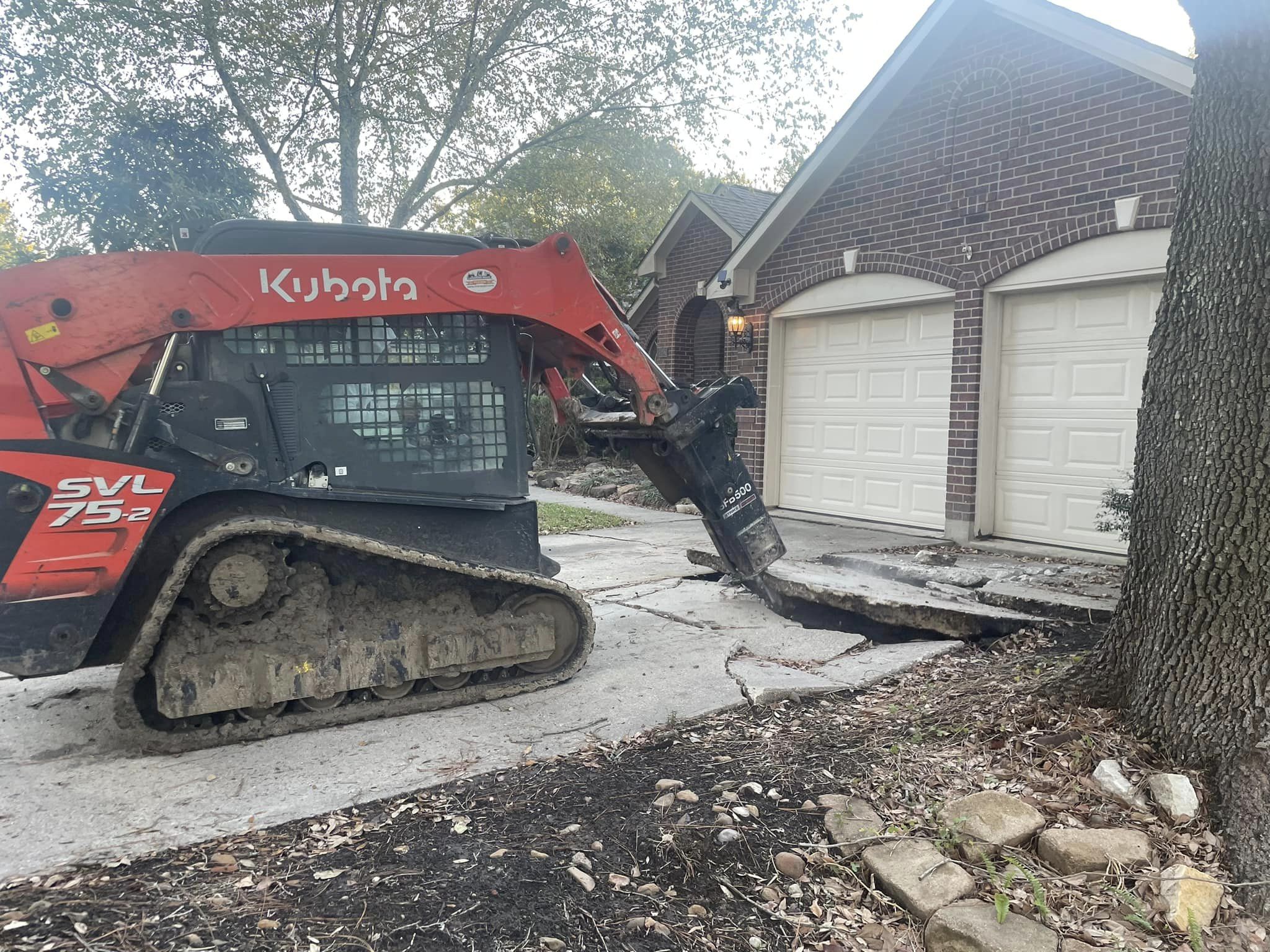
2. Sub-Base Materials
A stable sub-base (typically gravel or crushed stone) is essential. It provides a uniform foundation. It also improves drainage and prevents cracking. This material has its own cost.
Gravel or crushed stone is usually priced per ton or cubic yard. Delivery fees for aggregates also apply. Plan for 4-6 inches of compacted sub-base for most slabs.
Installation of the sub-base involves spreading and compacting the material. This requires labor and potentially a plate compactor rental. It's a critical investment for long-term slab performance.
3. Formwork Materials
Formwork defines the shape and thickness of your concrete slab. Materials typically include lumber (2x4s, 2x6s), stakes, and fasteners. These materials add to your overall project cost.
The complexity of the slab's shape will influence material needs. Curved designs require more specialized forms. Ensure your formwork is strong enough to hold the weight of wet concrete.
Reusable forms can save money on future projects. However, for a one-time residential slab, buying lumber is common. Accurate measurements prevent waste.
4. Reinforcement (Rebar, Wire Mesh)
Reinforcement adds tensile strength and helps control cracking. The cost depends on the type and quantity.
Wire Mesh: Typically less expensive per square foot. It's suitable for smaller slabs or areas with lighter loads.
Rebar: More expensive but provides superior strength for heavy-duty applications. Essential for foundations and a robust concrete driveway. Rebar chairs are also needed to position it correctly.
Calculate your reinforcement needs carefully. This material is a relatively small cost compared to the concrete. However, it significantly impacts the slab's longevity.
5. Concrete Pump Rental
If the concrete truck cannot directly access your pour site, a concrete pump truck may be necessary. Pumps can convey concrete over long distances or to elevated areas. They simplify placement significantly.
Pump rental fees are separate from concrete costs. They typically involve a minimum charge (e.g., 2-4 hours) plus an hourly rate thereafter. Prices can range from $600 to $1,000+ for a standard pump.
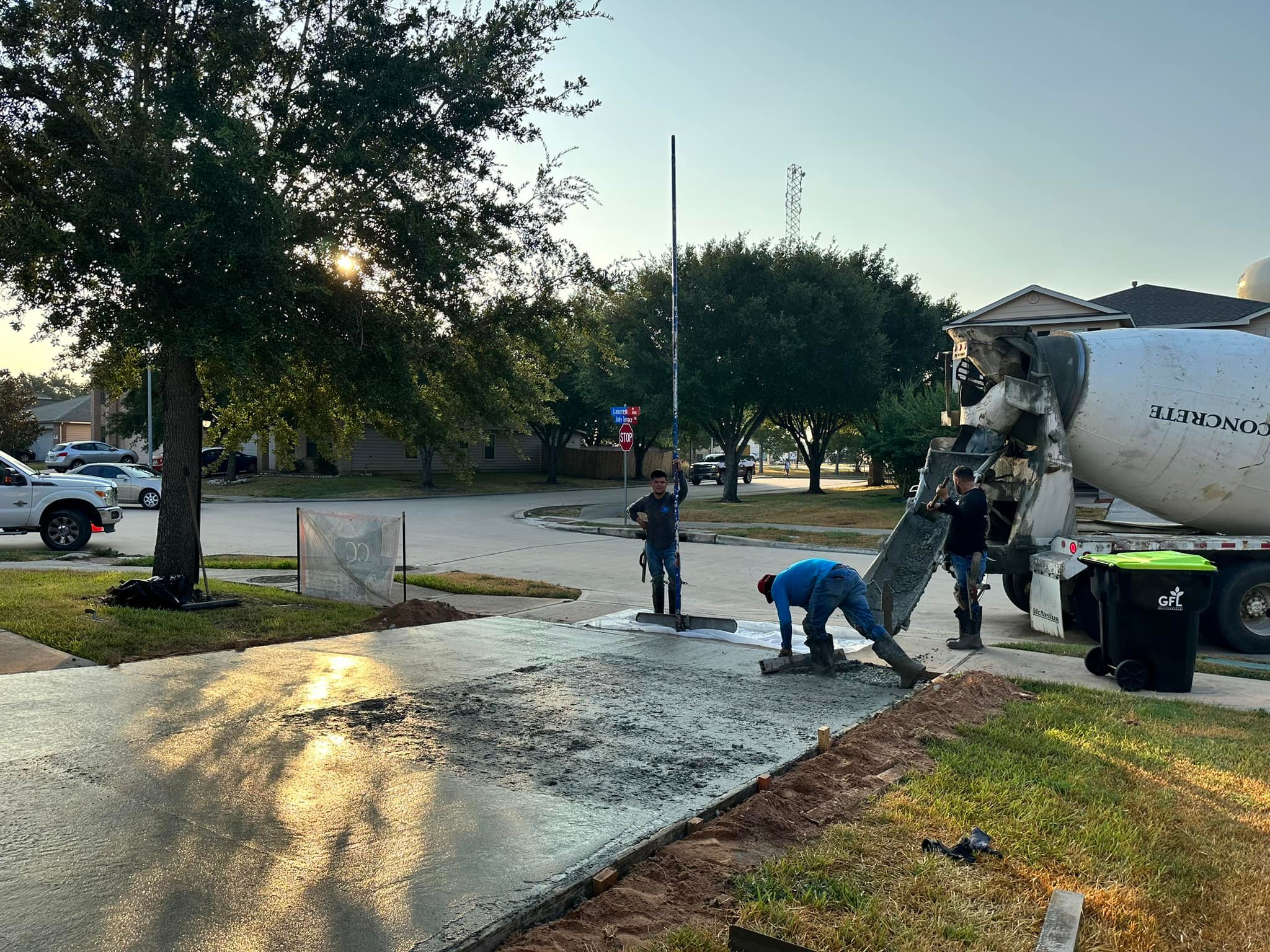
Consider the cost-benefit of a pump. While expensive, it can save considerable labor time and effort. It often prevents cold joints by speeding up the pour for large areas.
6. Tools and Equipment Rental
Unless you own all the necessary tools, you'll need to rent some equipment. This includes:
Plate compactor for sub-base.
Concrete mixer (if patching, not for a 10-yard pour).
Bull float, hand floats, edgers, groovers for finishing.
Wheelbarrows, shovels, rakes for spreading.
Rental costs vary. Factor these into your budget. Ensure you have the right tools for the job.
7. Labor Costs (DIY vs. Professional)
This is perhaps the most variable cost.
DIY: You save on labor but invest your own time and effort. You might still need to pay for helpers. Factor in your own expertise level.
Professional Contractor: Hiring a contractor includes labor, expertise, and their equipment. This is a significant part of the overall project cost. For a concrete driveway, professional installation is often preferred.
Professional installation ensures proper techniques. It often guarantees a higher quality finish. Contractors also handle permits and insurance.
8. Finishing and Sealing Materials
Beyond the basic pour, you might incur costs for:
Curing Compound: Essential for proper concrete hydration.
Decorative Finishes: Stamping, coloring, or exposed aggregate add significant costs per square foot. These are common for aesthetic enhancements.
Sealer: Applied after curing to protect the concrete from stains and moisture.
These optional enhancements can add considerably to the project's price. However, they can enhance curb appeal and extend the slab's life. They are a good investment for a new concrete driveway.
DIY vs. Professional Concrete Installation
Deciding whether to tackle a concrete project yourself or hire a professional is a critical decision. This choice significantly impacts cost, quality, and the overall project experience. For a 10-yard concrete truck delivery, the scale leans heavily towards professional involvement.
Challenges of DIY for 10 Yards of Concrete
Pouring 10 cubic yards of concrete is a very demanding task for a DIYer.
Sheer Volume and Weight: 10 cubic yards of concrete weighs approximately 40,000 pounds (20 tons). Moving and spreading this much material quickly is incredibly strenuous.
Time Sensitivity: Concrete sets rapidly. You have a limited window (often 60-90 minutes, depending on mix and temperature) to pour, spread, screed, float, edge, groove, and begin finishing. This requires a coordinated team.
Required Manpower: A 10-yard pour typically requires a crew of at least 4-6 experienced individuals. Without enough hands, parts of the slab will begin to set before they can be properly finished.
Specialized Tools: Beyond basic shovels, you'll need a bull float, hand floats, edgers, groovers, and possibly a power trowel for a large area. Renting and operating these takes skill.
Quality Control: Achieving a perfectly flat, smooth, or broom-finished surface with proper drainage is challenging for a novice. Mistakes are costly and difficult to rectify.
Liability and Safety: Working with heavy equipment and caustic concrete poses safety risks. Injuries are possible. Damage to property or utility lines could occur.
While smaller projects (like 1-2 cubic yards) are feasible for experienced DIYers, a 10-yard pour is generally beyond the scope of most homeowners. The risks of costly errors increase exponentially with volume.
Benefits of Hiring a Professional Contractor
For a 10-yard concrete project, hiring a reputable professional concrete contractor offers numerous advantages.
Expertise and Experience: Professionals have the knowledge to correctly prepare the site, choose the right mix, manage the pour, and achieve a high-quality finish. They understand local conditions. This includes handling expansive clay soils common in areas like Humble, Texas.
Proper Equipment: Contractors own or have access to all necessary tools and heavy machinery. This eliminates your rental costs and learning curve. They also have the pump trucks if needed.
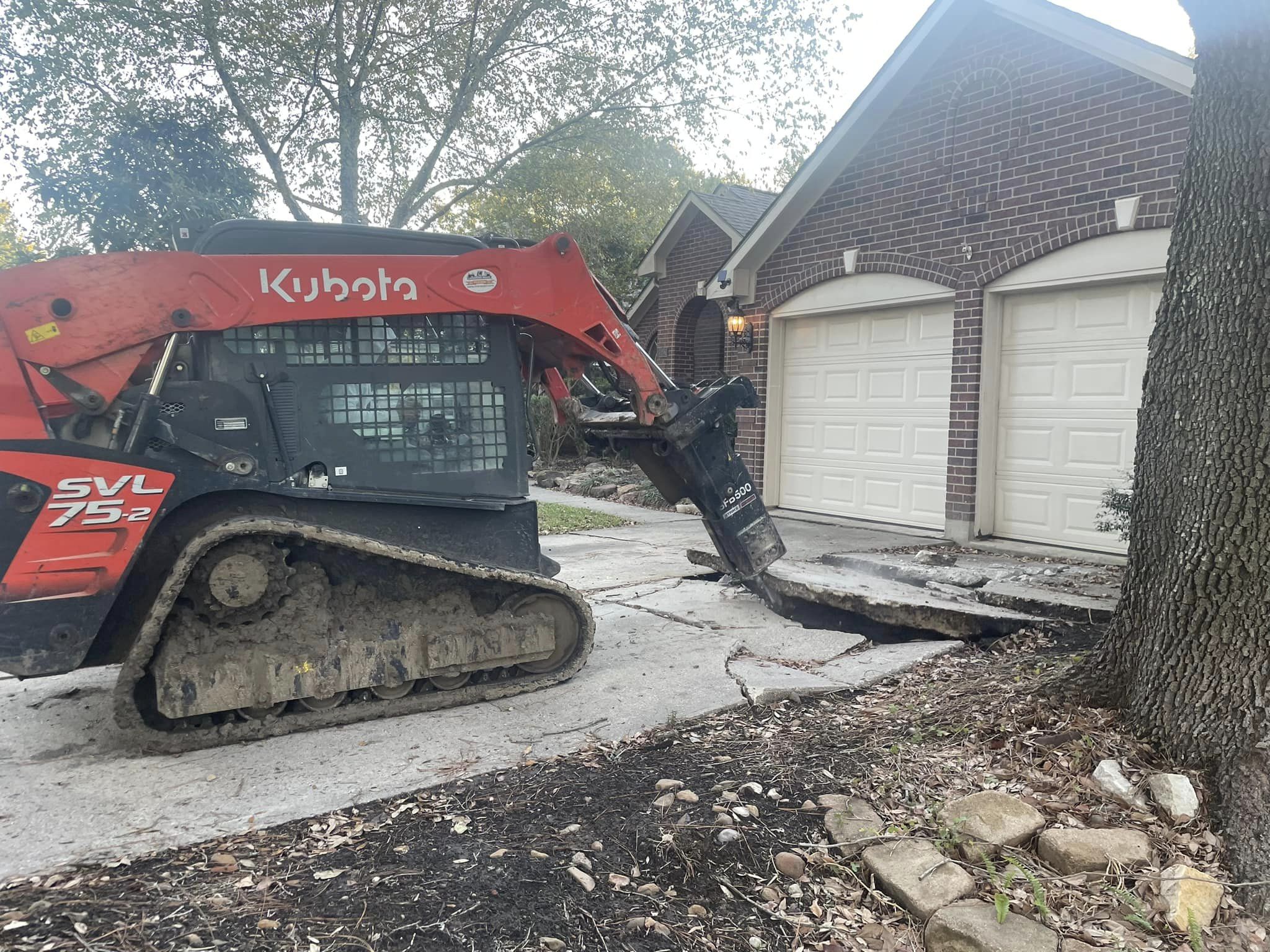
Efficiency and Speed: An experienced crew can pour and finish a 10-yard slab quickly and efficiently. This minimizes the risk of cold joints or uneven curing. They can manage large quantities of concrete.
Guaranteed Quality: Reputable contractors stand by their work. They often provide warranties. This ensures peace of mind regarding the slab's durability and appearance.
Permit and Code Compliance: Professionals are familiar with local building codes and permit requirements. They handle the necessary paperwork and inspections. This saves you time and prevents potential legal issues.
Reduced Stress and Labor: Hiring a professional eliminates the immense physical labor and stress. You can supervise the project rather than perform the demanding work yourself.
While the initial cost of a professional might seem higher, the long-term benefits often outweigh the savings of a DIY attempt. Especially for a project as substantial as a large concrete driveway or garage floor. A properly installed slab prevents future headaches and expenses.
Why Quality Concrete Matters
The investment in a 10-yard truck of concrete is significant. Ensuring the quality of that concrete is paramount. High-quality concrete, properly installed, provides long-term durability and performance. Skimping on quality can lead to premature failure and costly repairs.
Durability and Longevity
High-quality concrete, with the correct mix design and proper curing, will last for decades. It resists wear, abrasion, and environmental stressors like freeze-thaw cycles. This means fewer cracks, less spalling, and a longer lifespan.
A well-installed concrete driveway, for instance, can last 30-40 years. This longevity makes it a cost-effective choice over time. Inferior concrete might degrade much faster, requiring early replacement.
Structural Integrity
For slabs supporting heavy loads, like a garage floor or sections of a concrete driveway, structural integrity is non-negotiable. The correct PSI strength and proper reinforcement are essential. Quality concrete meets these structural demands.
It can withstand the weight of vehicles, equipment, and building structures. Compromised concrete can lead to sinking, severe cracking, or even collapse. This poses significant safety risks.
Resistance to Cracking
While all concrete can crack, quality materials and proper installation techniques minimize significant and unsightly cracking. Correct control joints, appropriate PSI, and good curing practices are key.
Fibers and admixtures in a quality mix also contribute to crack resistance. Preventing severe cracking maintains the slab's appearance and structural integrity. It reduces the need for frequent crack repairs.
Aesthetic Appeal
A quality concrete pour, especially with professional finishing, offers superior aesthetic appeal. The surface will be uniform, well-textured, and visually pleasing. This enhances your property's curb appeal.
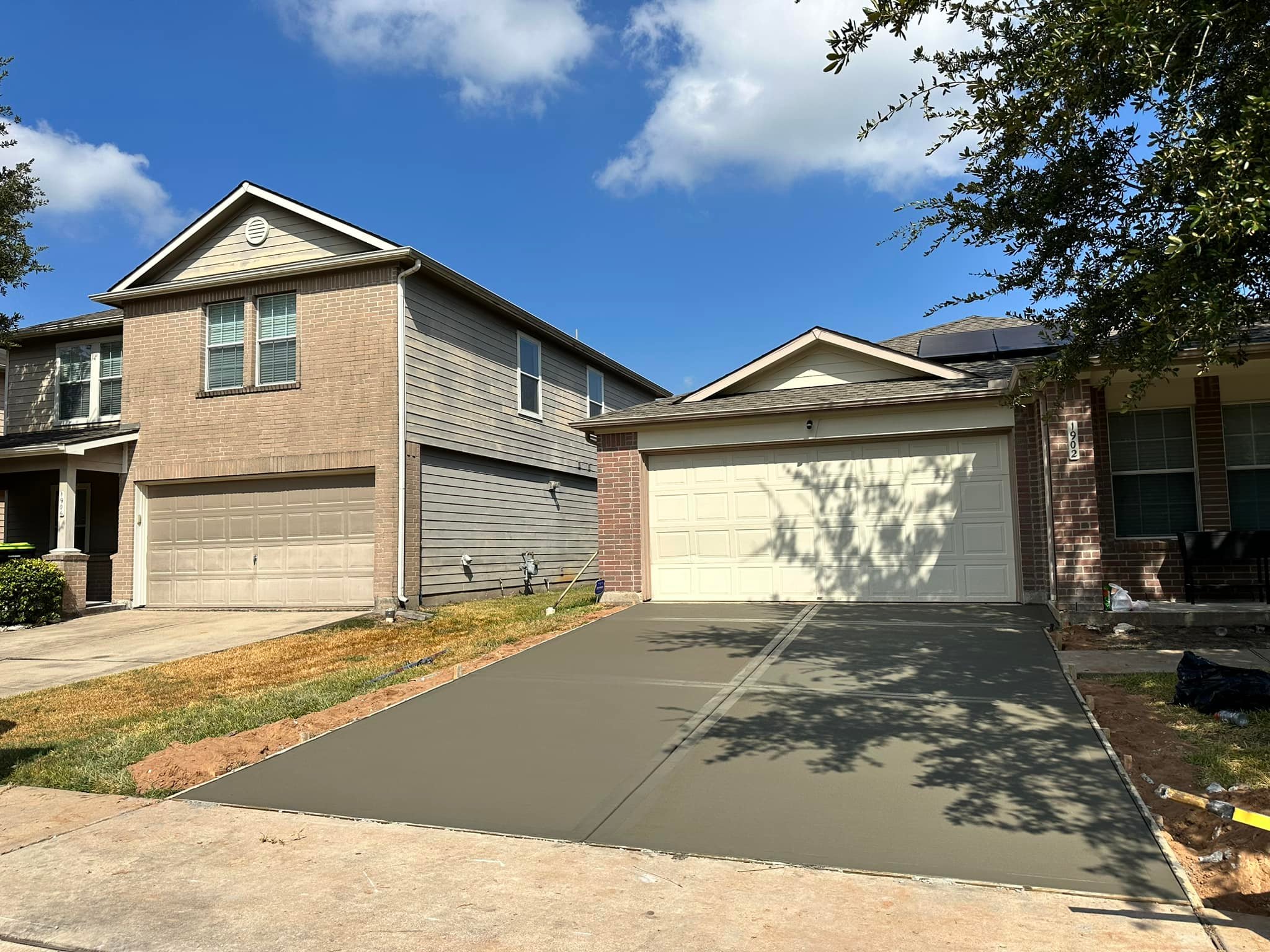
For decorative concrete applications like stamping or coloring, the quality of the base concrete is crucial. It ensures the decorative elements are properly applied and last over time. A poor base can compromise the decorative finish.
Return on Investment
Investing in quality concrete and professional installation provides an excellent return on investment. A durable, attractive concrete surface adds value to your property. It enhances functionality and curb appeal.
Choosing cheaper, lower-quality concrete or attempting a DIY project beyond your skill level can lead to premature failure. This results in the need for expensive repairs or replacement. Ultimately, this negates any initial savings.
Planning Your Project in Humble, Texas
For homeowners and businesses in Humble, Texas, local conditions and expert advice are crucial for any concrete project. From understanding soil types to navigating permits, local knowledge ensures success.
Local Soil Conditions
Humble, like many parts of Southeast Texas, is known for its expansive clay soils. These soils can swell when wet and shrink when dry. This movement can put stress on concrete slabs.
Professional concrete contractors in Humble understand how to mitigate this. They might recommend specific sub-base preparations. They may also suggest particular reinforcement strategies or thicker slabs. This accounts for local soil challenges.
Ignoring soil conditions can lead to premature cracking. It can also cause slab heaving or settling. Consulting a local expert is vital for long-term slab stability.
Permitting in Humble
The City of Humble and Harris County have specific regulations for concrete work. Depending on the size and nature of your project, permits may be required. This is particularly true for new structures or significant concrete driveway installations.
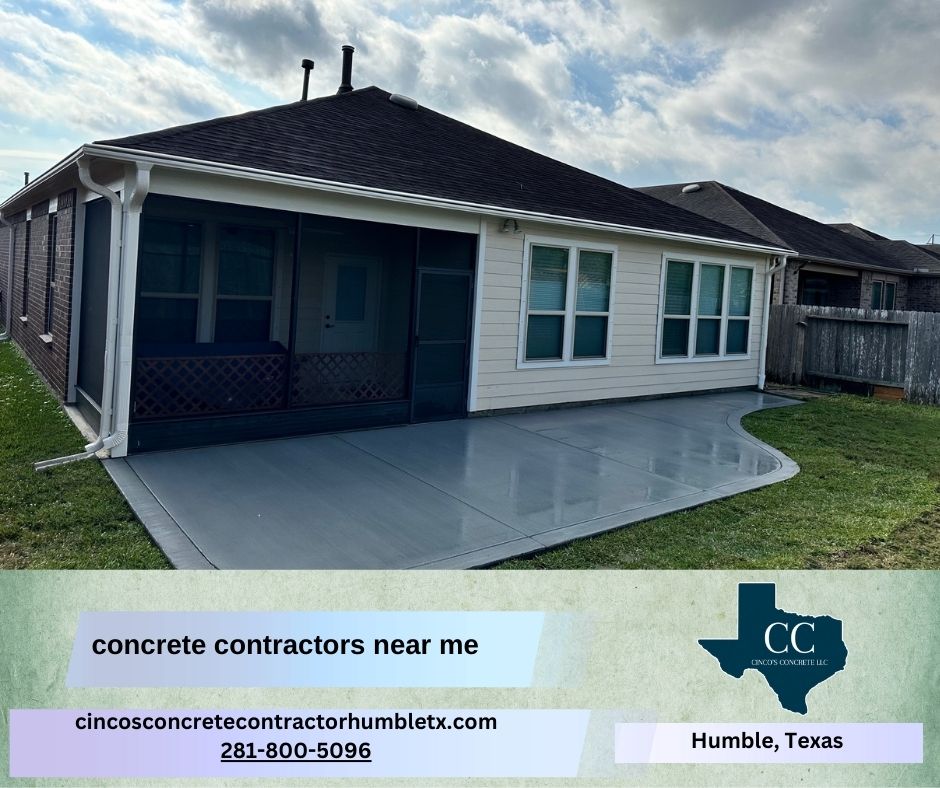
Always check with the City of Humble Building Department or Harris County Permit Office. Understand their requirements before starting. Failure to obtain necessary permits can result in fines or stop-work orders.
A reputable concrete contractor in Humble will be familiar with these requirements. They can assist with the permit application process. This ensures your project complies with all local ordinances.
Finding a Reputable Concrete Contractor in Humble
When dealing with a 10-yard concrete truck delivery, professional expertise is highly recommended. Choosing the right contractor is crucial. Look for:
Experience: Prioritize contractors with a proven track record of successful concrete projects in the Humble area.
Licensing and Insurance: Ensure they are properly licensed and insured. This protects you from liability in case of accidents or property damage.
References and Reviews: Ask for references from past clients. Check online reviews to gauge their reputation.
Detailed Quotes: Get written, itemized quotes from multiple contractors. Compare prices, but also understand what each quote includes.
Communication: Choose a contractor who communicates clearly and promptly.
For concrete projects in Humble, Texas, Cincos Concrete is a well-established and trusted choice. With over a decade of experience in the local market, they understand the nuances of concrete work in the region. They can provide accurate estimates for a 10-yard concrete truck. This ensures a high-quality finish for your concrete driveway, patio, or foundation.
Contact Cincos Concrete today for a FREE consultation and personalized estimate:
Phone: 281-800-5096
Website: https://cincosconcretecontractorhumbletx.com/concrete-driveways
Conclusion
The cost of a 10-yard truck of concrete typically ranges from $1,100 to $1,800, but this can fluctuate significantly. Factors such as concrete strength (PSI), the inclusion of admixtures, delivery distance, fuel prices, and regional market demand all play a role. Understanding these variables empowers you to budget accurately and make informed decisions for your project.
A 10-yard delivery is substantial, capable of covering large areas like a standard two-car garage slab, a large patio, or a significant portion of a concrete driveway. While a DIY approach might seem appealing for smaller tasks, projects involving this volume of concrete are best left to experienced professionals. Their expertise ensures proper site preparation, efficient pouring, quality finishing, and adherence to local codes.
Investing in quality concrete and professional installation provides long-term durability, structural integrity, and aesthetic appeal, ultimately adding significant value to your property. For residents in Humble, Texas, factoring in local soil conditions and permitting requirements is also vital for a successful outcome.